Producing packages for radioactive materials takes time, attention to detail, and a thorough commitment to quality assurance.
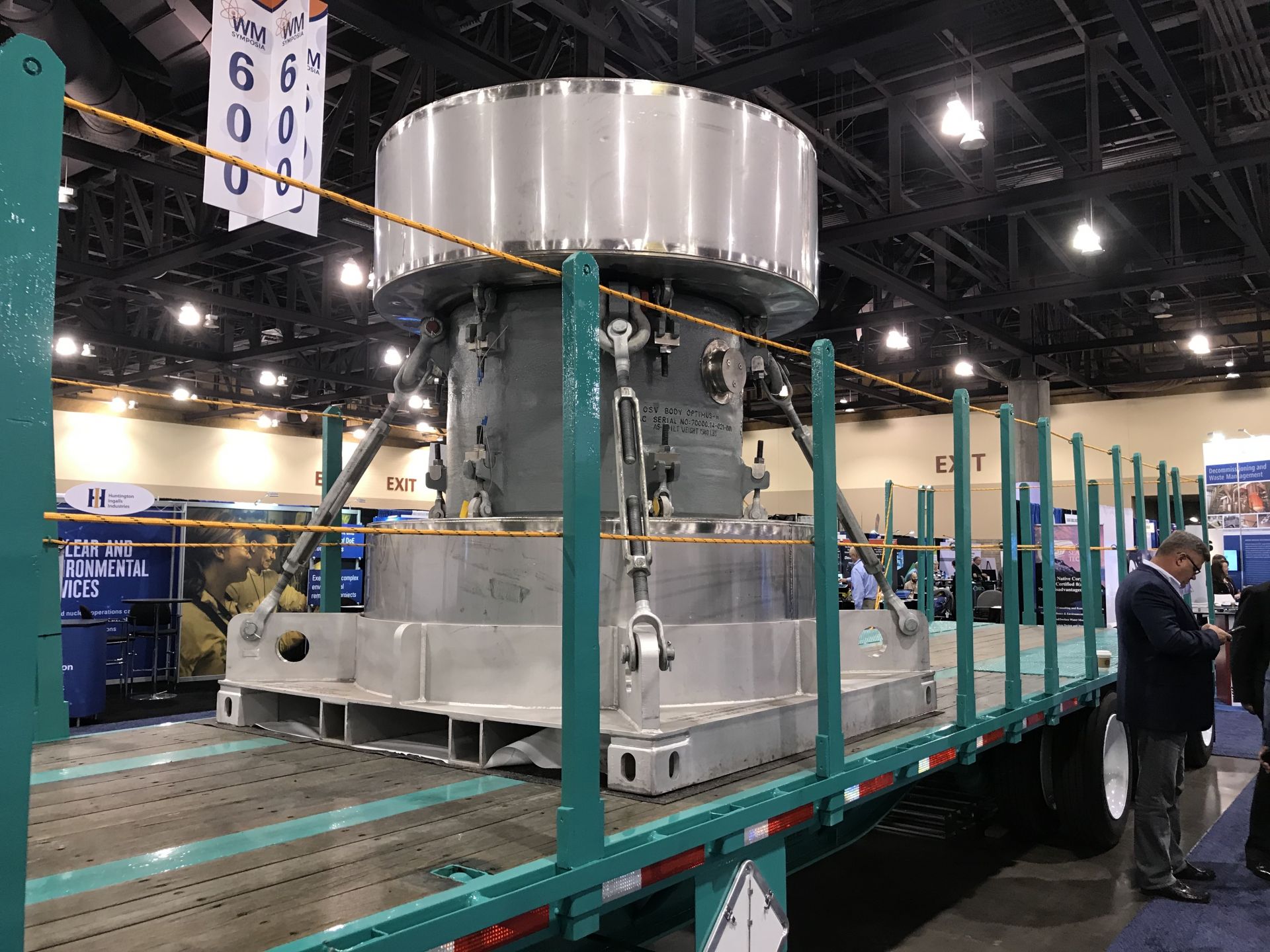
The Optimus-H transport cask on display at the 2020 Waste Management Conference in Phoenix, Ariz.
Jeff England, director of transportation projects for NAC International, pointed to the large stainless steel canister, which looked like a giant-sized silver dumbbell, perched on the flatbed of a semitrailer truck parked in the middle of the expansive exhibit hall in the Phoenix Convention Center. NAC, a provider of nuclear storage, transportation, and consulting services, was using the 2020 Waste Management Conference, held March 8–12 in Phoenix, Ariz., to unveil its newest transport casks, the Optimus-H and Optimus-L.
“These are a different niche,” England said of the casks, which were designed to transport radioactive materials, including remote-handled transuranic waste, high-activity intermediate-level waste, low-enriched uranium, and fissile materials. “You have a lot of [small] drum-sized packages, and you also have a lot of big packages that will hold around 10 55-gallon drums. But there’s not anything in between. We hold a 110-gallon drum capacity.”
Thinking outside the box, the nuclear sector puts a new spin on a pharmaceutical tool.
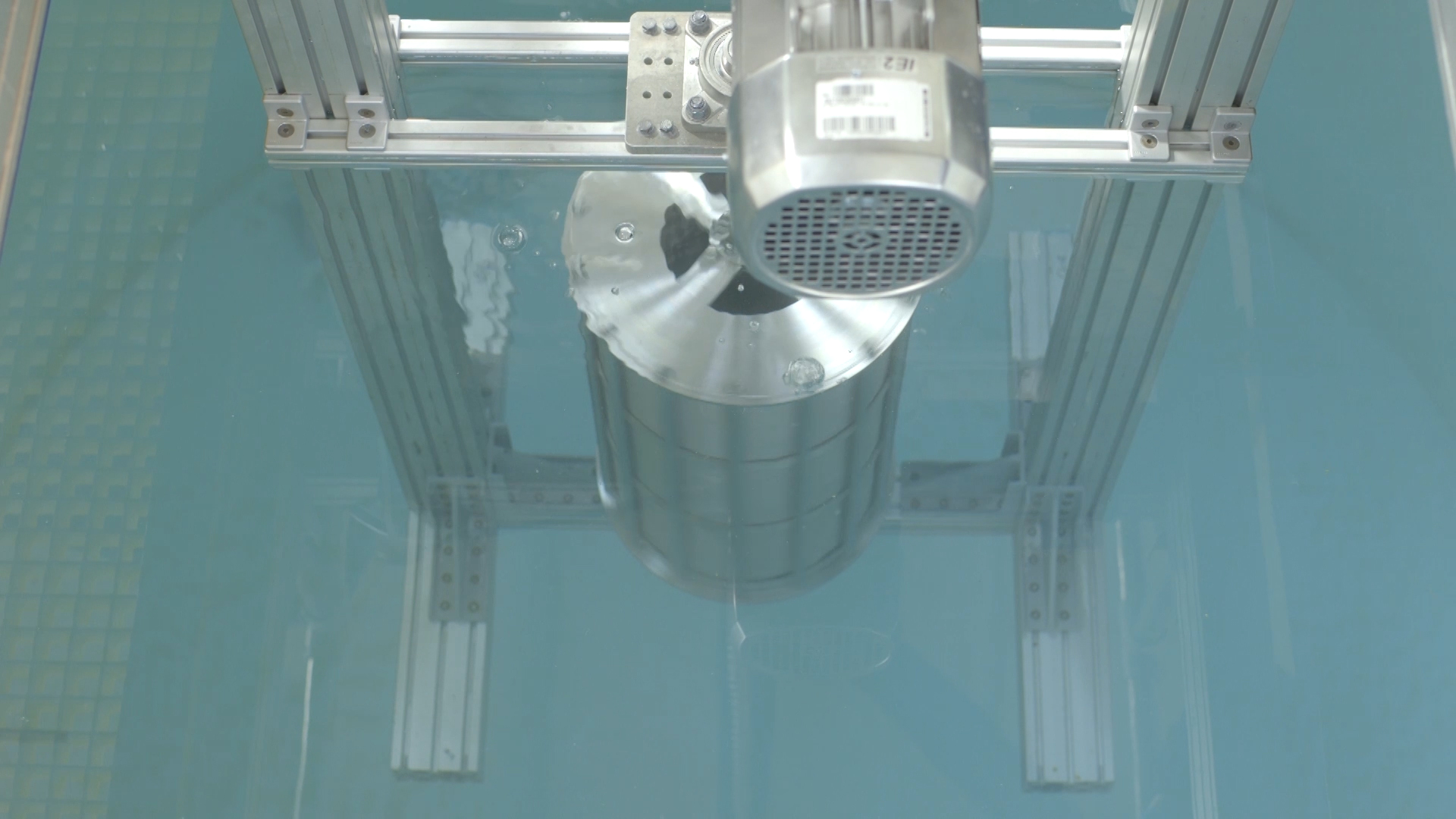
Large-scale testing is done on the Spinionic rotating bed reactor system.
We live in a world where we are continually driven to increase efficiency while decreasing costs—to do more with less. The nuclear industry is no different. Developing innovative techniques or adapting creative ideas found in other industries can support that pursuit to reduce cost and, in this case, volumes of waste, while providing program certainty. Such actions build confidence in our industry and allow nuclear power to continue to be part of the narrative of our clean-energy future.