Colin Judge: Testing structural materials in Idaho’s newest hot cell facility
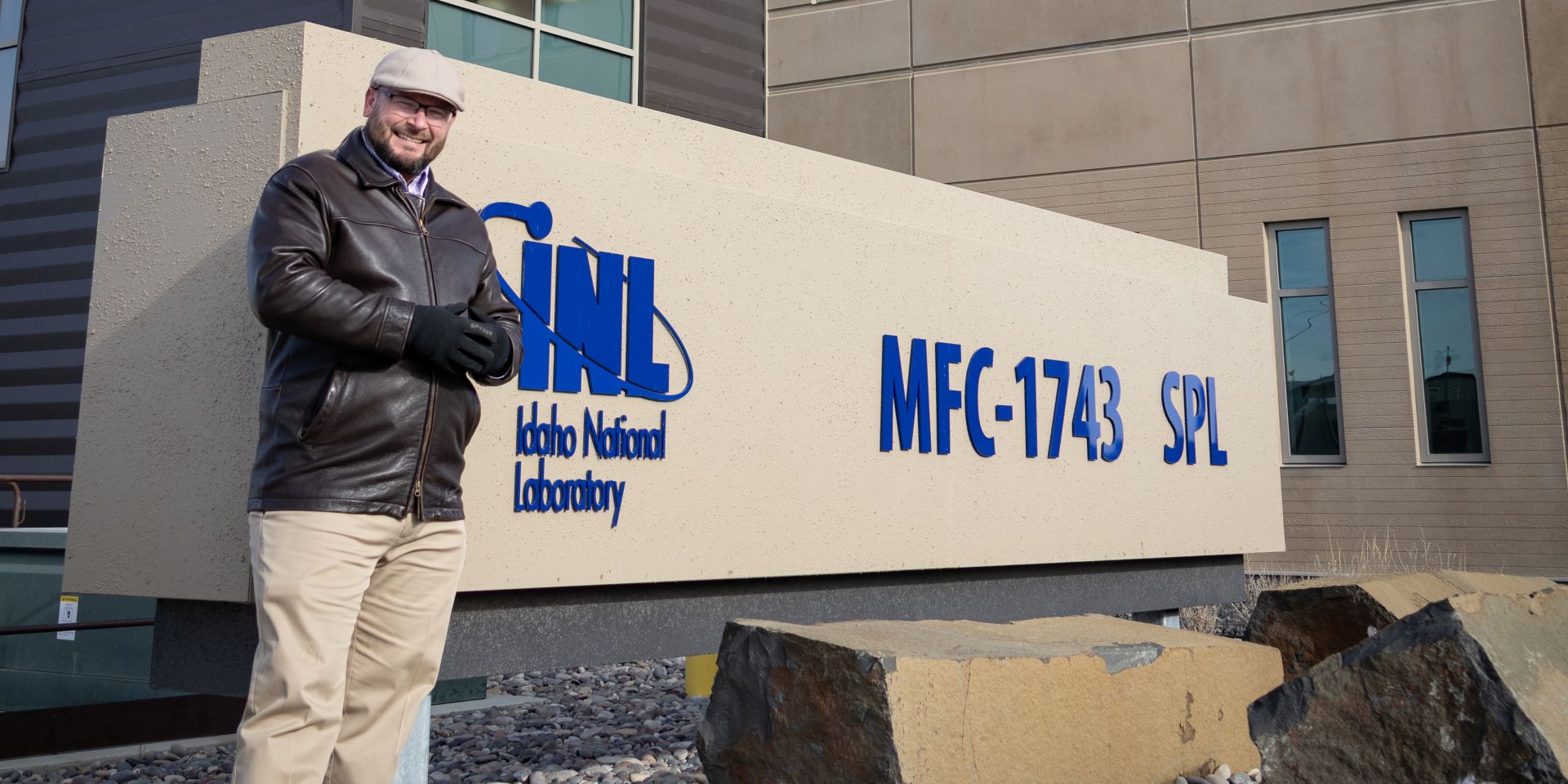
Idaho National Laboratory’s newest facility—the Sample Preparation Laboratory (SPL)—sits across the road from the Hot Fuel Examination Facility (HFEF), which started operating in 1975. SPL will host the first new hot cells at INL’s Materials and Fuels Complex (MFC) in 50 years, giving INL researchers and partners new flexibility to test the structural properties of irradiated materials fresh from the Advanced Test Reactor (ATR) or from a partner’s facility.
Materials meant to withstand extreme conditions in fission or fusion power plants must be tested under similar conditions and pushed past their breaking points so performance and limitations can be understood and improved. Once irradiated, materials samples can be cut down to size in SPL and packaged for testing in other facilities at INL or other national laboratories, commercial labs, or universities. But they can also be subjected to extreme thermal or corrosive conditions and mechanical testing right in SPL, explains Colin Judge, who, as INL’s division director for nuclear materials performance, oversees SPL and other facilities at the MFC.
SPL won’t go “hot” until January 2026, but Judge spoke with NN staff writer Susan Gallier about its capabilities as his team was moving instruments into the new facility.
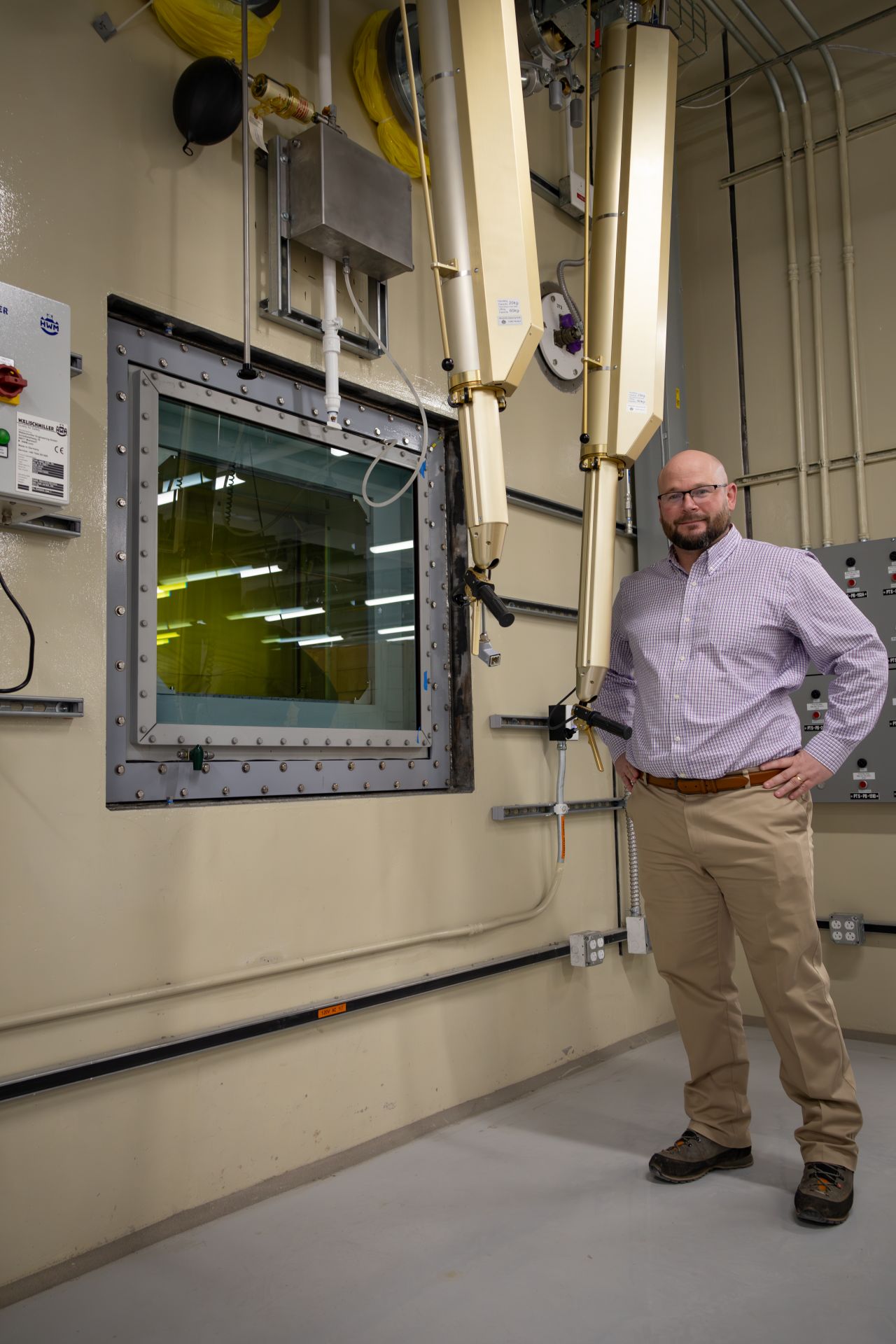
Judge at a hot cell window in SPL. (Photo: INL)
You began your career in materials science at Canada’s Chalk River Laboratory. What’s your current role at INL, and how did you get there?
I am the division director over nuclear materials performance, which includes management and operations of our nuclear facilities. We try to understand materials. We break them down to fundamentals and then pull that data back up into the engineering scale as we link it to operability in a nuclear reactor.
How I got here is a much longer answer. I am Canadian, and I joined Atomic Energy of Canada in 2008, working at Chalk River for the organization now known as Canadian Nuclear Laboratories. I’ve always worked on the mechanical engineering side of material science. I’m going to take something from a reactor, I’m going to break it, and then I’m going to try to understand why it broke and what the limits of the material are. I did this in Canada for over 10 years, using instruments at Chalk River but also here in Idaho, before I joined INL in 2019.
In Canada, they operate largely like a commercial lab. They get money from the federal government, but much of what they earn is commercial revenue. When I came to Idaho, I tried bringing that same flavor into work with INL. We started doing a lot more advanced reactor work, and my experience with industry helped. I started as the industry liaison for the Nuclear Science User Facilities.
But my heart and soul has always been in materials characterization using advanced microscopy techniques. When a division director role opened here at the MFC, I applied and came into that role almost four years ago now.
What makes SPL unique?
SPL under construction in 2021 (top) and 2023 (bottom) at the MFC. (Photos: INL)
We started construction of the Sample Preparation Laboratory in 2020, but planning began almost a decade earlier. It’s been some time since we’ve built a new hot cell, so we wanted to design something for the future, taking advantage of new systems, robotics, cameras—everything that we’ve learned over a half-century of research in the Department of Energy.
The SPL is a non-alpha facility. Irradiation experiments at our ATR typically have gone from the ATR to our HFEF, which has one of the largest open area hot cells in the world. We would then unpackage it, process it, and test the material. The complication is that HFEF is highly contaminated with alpha radiation after decades of experimental work with irradiated fuels. When even nonfueled test samples pass through the HFEF, it limits where we can send that material, because a lot of partner facilities—including national lab neutron beam centers or university labs—cannot manage alpha-bearing or alpha-contaminated material.
One of the big things that SPL is going to do is enable us to receive material directly from ATR for nonfueled experiments and unpackage it, process it, cut it down, and send it out for research. We want people to see us as an extension of what they have and see how we can help their facilities excel.
Where are you now in the commissioning of SPL?
We’re aiming to go hot in January 2026. The building is complete, and we had a ribbon-cutting event in the fall. Scientific staff are moving into the facility with our technical operators and our operations team in January 2025. In mid-December, we started installing some of the scientific equipment and robotics. The manipulators are almost complete.
This next year of work—in 2025—is installing equipment and going through our operational readiness and management safety assessment. We’ll be testing all of the science equipment, all of the microscopes, and the robots with nonirradiated materials, but as if they were radioactive. We will ask some challenging questions about “what if” scenarios and justify it to ourselves that we have addressed how we would respond. For example, what if you drop a sample? What does that mean and how would you recover? What if you lost power to your camera systems in a hot cell with no windows—what’s your recovery pathway? We’re going to be answering those questions so that when we go hot, we don’t have surprises.
What are some ways SPL can support nuclear power?
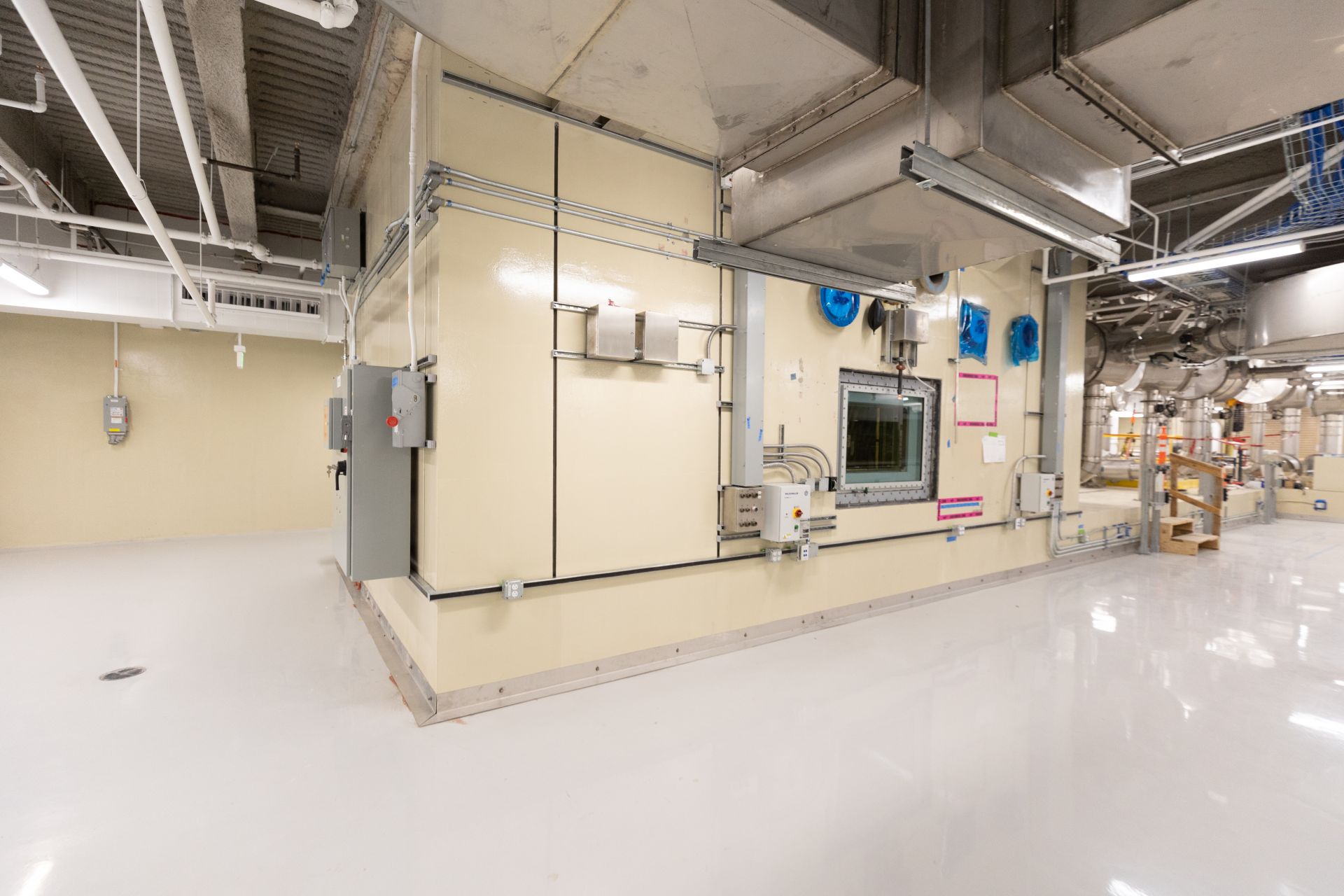
A material transfer cell where the casks mate to the hot cell, during construction (top) and after (bottom). (Photos: INL)
Some of the newer capabilities we’ve introduced into SPL will help us explore unknowns for structural materials for advanced reactors using molten salt or gas as a coolant material. We have a few areas within SPL that we call experimental test beds. These shielded enclosures will allow us to move an experiment in for a short-term testing campaign. Somebody who needs to test things in extreme environments can wheel in a molten salt corrosion loop, execute for six months, do their experiment, then move it out, leaving the hot cell space ready for the next experiment. You don’t need to put in an experiment that is going to take up space for 10 years.
SPL was designed to give us additional floor space with flexibility. If we have somebody new come to us in five years who has an amazing idea, we can enable it because we’re not going to be busting at the seams on our floor space.
We also plan to receive light water reactor material directly from utilities or via the Nuclear Regulatory Commission or the Electric Power Research Institute, turning a decommissioned reactor into a source of irradiated materials for experiments. We’ll cut into components we typically don’t get to see, save them on behalf of the DOE, and then we can size, grind, and polish from there.
Will SPL do any fuel testing?
SPL will be looking at structural components, including fuel cladding, metallic components, maybe some ceramic components, but not fuel itself. Right now we’re doing all of the structural material work and the fuels work in our fuels labs. By having a new hot cell that’s only for structural materials, I can segment those activities—optimize the fuels hot cells and optimize the structural hot cells so we can do more.
The thing is, a lot of these materials have been tested, characterized, and understood for nonirradiated conditions. Not many of those materials have been placed in a nuclear reactor with neutrons and then tested after we’ve irradiated them. So there’s some work to be done to better understand these materials after they have been irradiated.
To what extent can materials be characterized at SPL versus prepping the samples to be characterized elsewhere?
Our name is the Sample Preparation Laboratory and preparing samples to send somewhere else is part of our mission. But that’s not our only mission. I think if we called it a structural properties lab, that would help explain what we do.
I can clarify by stating that SPL is not a fuels lab. We are everything else beyond that—structural properties and structural materials. Part of what we do can enable others to test materials, but we are also equipped for mechanical testing within SPL. We can break components and then use advanced microscopy tools to try to understand why they broke. And then we work with our counterparts in modeling and computation to then link that back to performance in a reactor.
We are working with our partners to determine what corrosive environments to test. We are going to have systems exploring material properties at higher temperatures with molten salt, for example. And then looking at the impacts of helium or hydrogen on materials has relevance for high-temperature fission reactors as well as fusion. We are focused on materials almost regardless of reactor design.
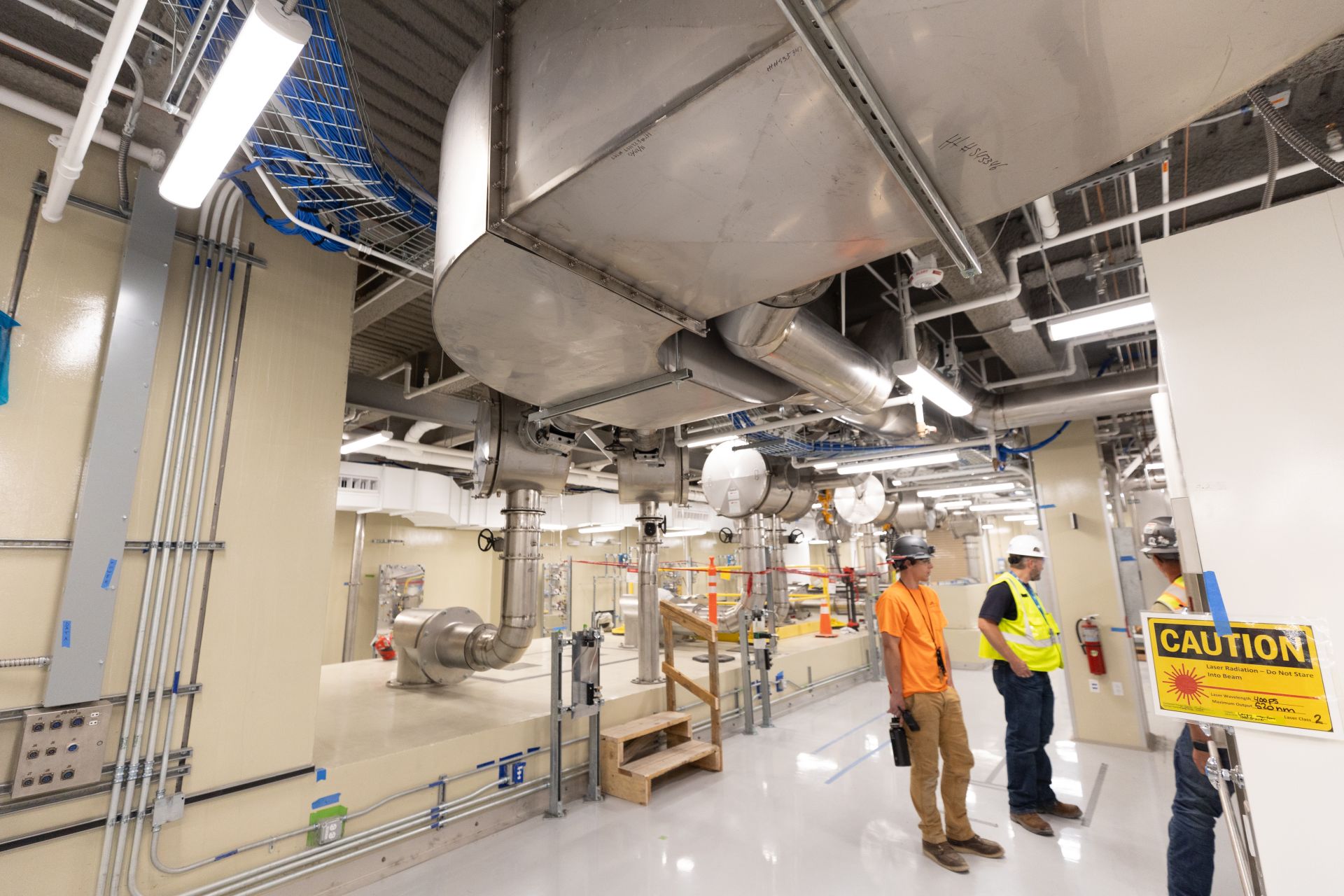
Equipment installation underway at SPL. (Photo: INL)
So you’ll be subjecting materials to extreme conditions in SPL? You won’t simply process samples that have been exposed elsewhere?
Yes. When we do experiments to understand performance, irradiation is one part of it, but when we take the irradiated material and then subject it to either high-temperature testing or high-temperature testing in a corrosive environment, we can get a better sense of degradation mechanisms and how they are breaking apart or withstanding that degradation. In an ideal world we want everything to withstand everything, so in many cases we look at those limits and try to design better materials, such that they’re not subject to degradation.
The reality is when you take materials of any sort and put them in an extreme environment like a nuclear reactor, they change. What makes it safe is that we understand what’s taking place and there are no surprises.
How are samples moved and tested within SPL?
We use pneumatic transfer tubes—like old bank tubes—to shoot samples across the facility. These are all tied into the main hot cell, and all our shielded enclosures are direct-coupled to that.
In those shielded enclosures there are dedicated robots that will load from the pneumatic transfer into our systems. We have three shielded enclosures, one of which is the experimental test bed we already discussed.
The second has an XRD (X-ray diffraction) capability and a secondary electron microscopy tool with a dual-beam focused ion beam (FIB) as a small-scale machining tool. You can ablate material away and obtain very small volumes of material and put them into other microscopes for study—or even test subsize tensile specimens and mechanical test specimens.
The system in the third enclosure is X-ray photoelectric spectroscopy (XPS) for surface science. If we have a different oxide after exposing materials to high temperatures in molten salt, and we want to identify what oxides are forming and how the material is degrading and corroding, we can use XPS to determine if it is a protective oxide or if it is going to degrade and lead to localized corrosion that can then fail a component.
What are the benefits of small test samples?
Once we FIB specimens that are very, very small—you can go down to very thin 10 micron by 10 micron specimens—and if the only source of radiation is beta or gamma, then at that volume it’s below a threshold that is identified as de minimis. It’s not negligible, but I can put it into a package and ship it across the United States without external labeling because it’s not a hazard. Most universities can handle that in the United States and in Canada.
Or we can just move the material next door to our Irradiated Materials Characterization Lab (IMCL), where we have what I would say is the most complete capabilities at a nuclear facility in one building dedicated to doing advanced material characterization and testing.
You’ve mentioned robotics and automation in SPL. Did you need to bring new and different experts to INL to build those capabilities?
The idea of robotics in a hot cell was something that was part of the original concept and design for SPL. Radiation tends to break down electronics, so the thought of having a hot cell with cameras that break down and robots that break down was a risk. The cells that have them don’t have a large inventory of material, so it’s not continuously getting bombarded. We will have to go through preventative maintenance and planning and monitoring, and we can swap those systems out as necessary on whatever frequency we determine.
The main robot in our mechanical property test cell looks like the robot from Lost in Space. It translates vertically, it rotates, and it has two arms, and you can operate this and move it around much like you would a typical manipulator in a hot cell. Or you can operate it with what looks like a video game controller. Getting operators trained in that space is something that we’ve already started doing. We can show research sponsors what we’re doing with those robotics live—so you can see and observe what we’re doing without having to come to Idaho.
We did have to establish some new expertise. We’re trying to incorporate AI and machine learning into those systems so that we can push the limits on semiautonomous and autonomous robotics.
Do you have companies lined up ready with work once SPL goes hot?
Yes. We have clients, and we have DOE-sponsored programs and activities. The Nuclear Science User Facilities is going to have some activities coming into the facility on day one. We have some advanced reactor vendors—I’m not going to name who—that are looking at some metallic components and metals that are already code qualified, but they want to characterize them in different scenarios and environments to build their licensing case. And then we have a few that we’re in talks with right now for how we can optimize work in those experimental test beds.
Something I really want to clarify is that we are not just a “come to us, test it, and here’s your data” lab. Sometimes people don’t know exactly what options are available. We can help them shape their programs with our experience and our background in this area.
We have a few sponsors we’re working with now on what type of tests they’re going to want. Some of them are mechanical, so just pure tensile properties. Some are creep properties, so how is the material deforming under a low load over high temperature but longer times? And then others are cyclic, where you’re loading either the temperature cycling or mechanical cycling, putting a sample through tensile and compressive cycles, and kind of pushing the materials to the extreme.
What do different reactor operators or developers want to learn, if it’s possible to generalize?
I can make it really easy. They’re interested in money, and they’re interested in safety. You want to make sure that the reactors are operating efficiently and safely.
Some current reactor operators want to maintain operability to 80 or 100 years. The longer they can operate without having to build a new reactor, good for them. We’re kidding ourselves if we think it doesn’t come down to economics and whether people are going to make money. But they have to do so safely.
I don’t want to speak about specific challenges and issues that I know some of them are working through, but you’re looking at pushing the materials through their limits. When you’re hitting materials with irradiation, typically they saturate at a certain level and properties don’t change. That takes place very early on in the life of a reactor—three to five years operating at 300°C. But corrosion can change with time if the material is degrading. I think they have a good handle on that for LWR technologies now. So we’re really just helping them maintain the safety of their components.
When it comes to advanced reactors, you have to know what you know, try to know what you don’t know, and hope you don’t have many unknown unknowns. When you go to higher temperatures, your properties don’t necessarily change, but you can see phase transformations in materials operating at higher temperatures for a long time. You’re going to see mechanisms, like thermal creep, that don’t typically occur at 300°C. We can offer materials test data that can help those advanced reactor vendors develop a licensing case.
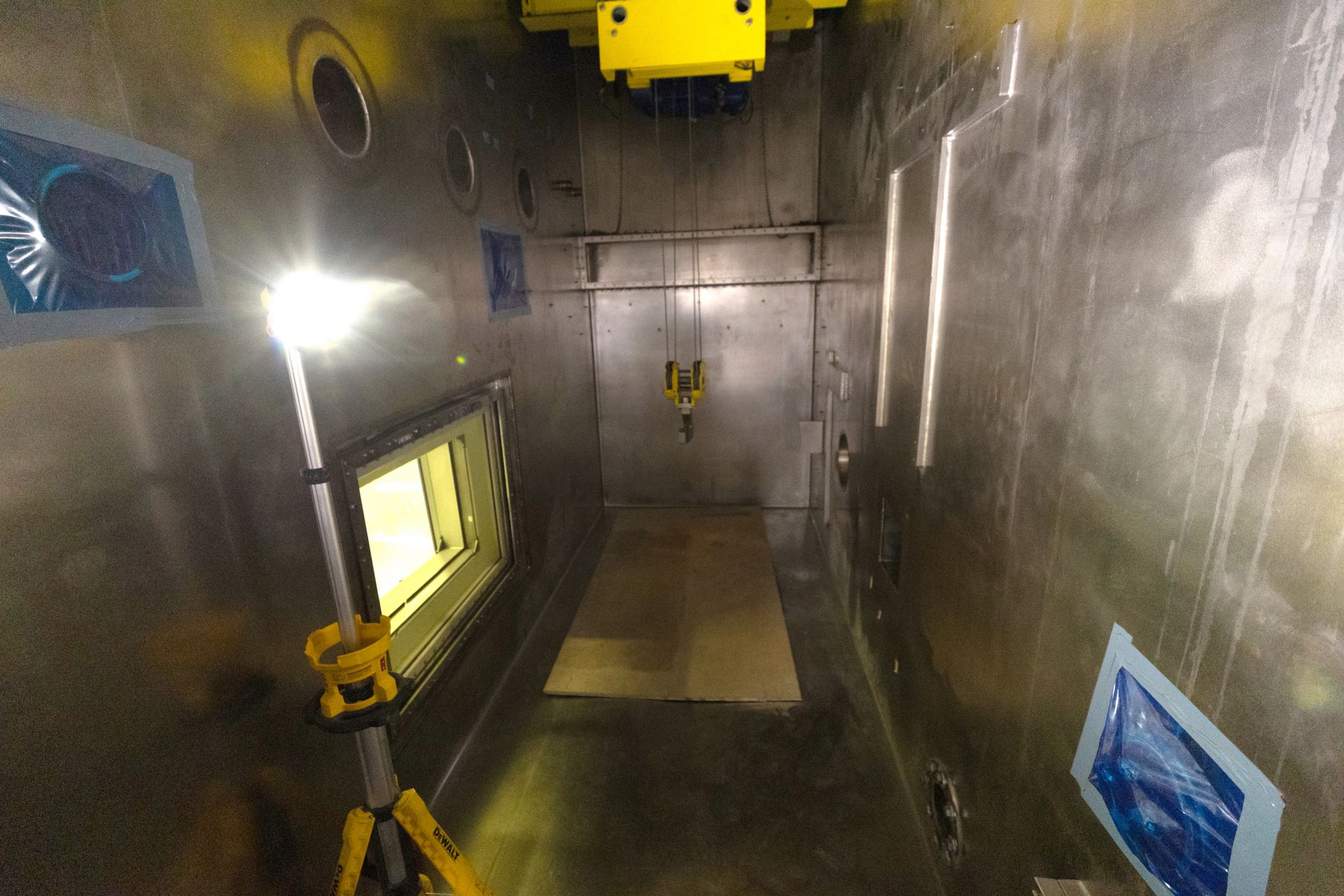
The view from inside a not-yet-hot hot cell in SPL. (Photo: INL)
How can SPL test materials for fusion applications?
In many cases there’s overlap with fission. You’re at higher temperatures and in an environment where you’re going to have helium either forming on the material or diffusing through the material. You have hydrogen. When you start talking about gas formations in material, it’s either coming from irradiation or from the environment. In a fission system, thermal neutrons interact with a material and you can get transmutations that lead to cobalt, hydrogen, iron, and helium forming inside the metal. Hydrogen tends to diffuse relatively easily through a metal, and as it does that, it breaks the inner atomic bonds and allows dislocations to move through the material much faster. So it enhances plasticity and deformation. You get hydrogen coming from inside or you get hydrogen diffusing from the outside through corrosion. Understanding how that works is a real problem. I always say—if in doubt, blame hydrogen.
Helium enters a material through transmutation neutrons, but it can also enter through the natural decay of tritium. So the question is, does that lead to embrittlement? Does that limit the threshold on either fracture toughness or tensile properties? Those are things that are going to impact both fission and fusion, and SPL can absolutely impact that science.
How do you see SPL fitting into the full scope of nuclear work at the national laboratories?
I had the fortune last year of being part of the Oppenheimer Science and Energy Leadership program. Our cohort traveled to every DOE national lab in the United States in one year and we spoke with lab leaders and looked at challenges and issues. A common theme emerged. It’s two made-up words, but they sit with me: “coopetition” and “competeration.”
The DOE labs have to cooperate. But naturally, there is a little bit of competition too. We work together, but we also compete for staff and funding. I try to keep an open and outward mindset and recognize that we’re going to have to work together.
With SPL, INL now has fuels facilities and structural facilities. Other labs also have structural material capabilities, but it’s not duplication. Largely, the question is how we enable the U.S. goal of tripling nuclear capacity by 2050. We cannot do that in isolation, and we have to do things much faster. The only way we’re going to do it faster is by collaborating and using SPL as a centralized hub to send things out to other labs, even if it’s something we can do at INL. We can do it a lot faster if I send half the samples to you and we work together to analyze the data. So I want people to see this facility as one that can enable them, not one that’s going to compete against them.
Susan Gallier is a Nuclear News staff writer focusing on research and applications of nuclear science and technology.