In a recent study published in Nature Scientific Reports, Argonne scientists introduced a method to identify microscopic defects in stainless steel parts produced through additive manufacturing, a process that includes 3D printing. While this technology can create complex metal components, it can also introduce tiny defects—such as pores—that compromise material strength. These flaws, often smaller than a human hair, can weaken metal parts that are intended for harsh environments like nuclear reactors. Thanks to Argonne’s approach, detection of these deficiencies has become more precise than ever.
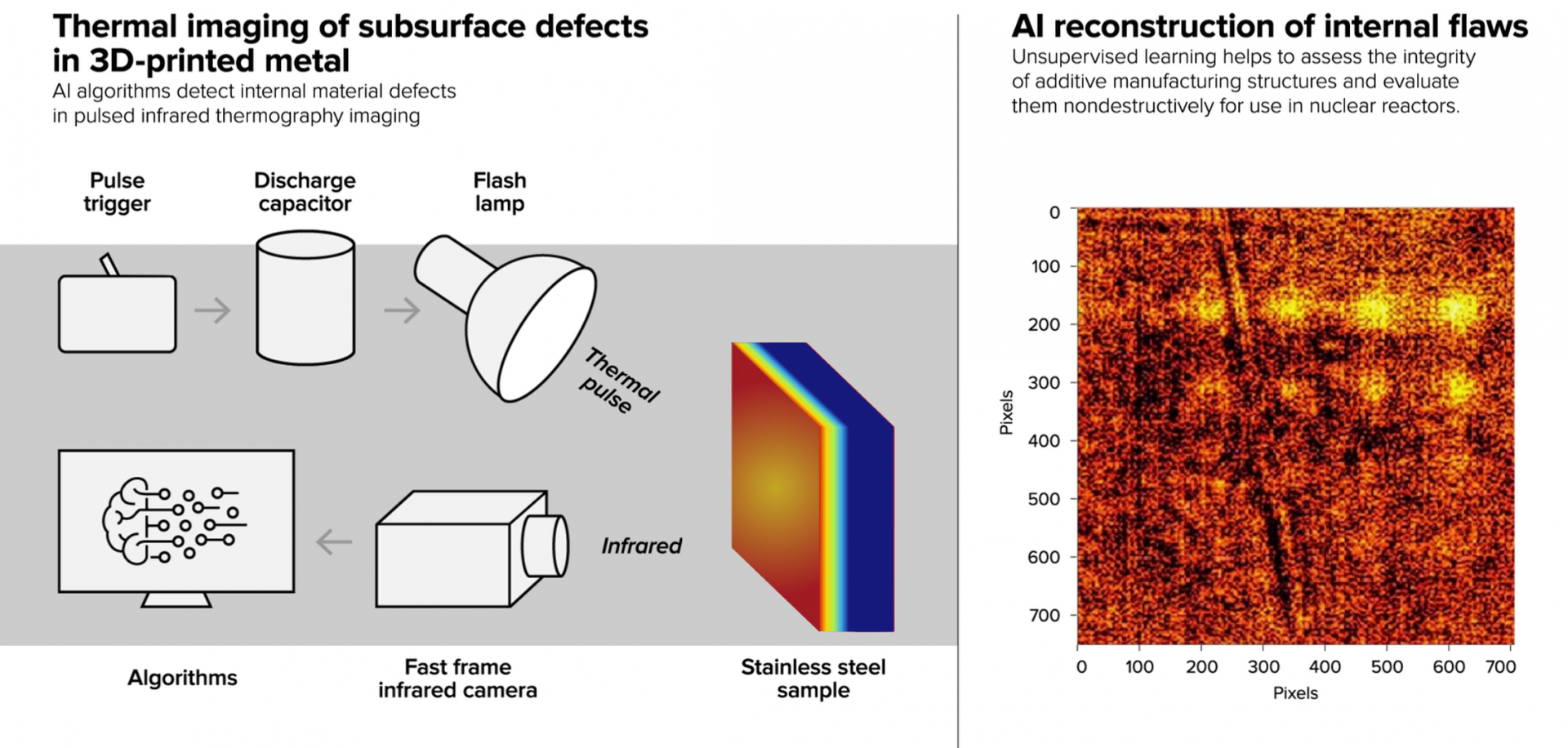
AI algorithms detect internal material defects in pulsed infrared thermography imaging. This helps to nondestructively assess the integrity of 3D-printed structures for use in nuclear reactors. (Image: Argonne National Laboratory)
Enhancing detection
The scientists combined a technique called pulsed infrared thermography (PIT) with AI to detect the microscopic defects in stainless steel. PIT rapidly heats the surface of the metal with an optical flash lamp while a fast-frame infrared camera measures how surface temperature decays as the heat diffuses into the material bulk. Internal flaws, like air-filled pores, alter the material’s thermophysical behavior, making it harder for heat to pass through smoothly.
Images obtained with PIT contain information about material defects. However, identifying these subtle features is challenging, as the images can be distorted due to thermal noises and blurring because of heat diffusion.
Fortunately, AI can play a vital role in detecting small features in images. The researchers developed an AI algorithm that processes the thermal images from PIT. This algorithm filters out noise and enhances the visibility of defects, allowing for the detection of flaws as small as 100 microns in diameter—significantly improving on previous methods.
“Our new approach allows us to identify these tiny defects that were previously undetectable using conventional approaches,” said Alexander Heifetz, lead researcher. “This is an exciting step forward in ensuring the integrity of structural materials used in nuclear applications.”
A breakthrough
Additive manufacturing, which incorporates 3D printing techniques, is increasingly popular for producing parts used in extreme environments, such as inside nuclear reactors, where metals must withstand high heat and radiation. The long-term strength and reliability of these components depend on the detection and prevention of defects.
Traditional nondestructive defect detection techniques, such as X-ray imaging and ultrasonic testing, struggle to identify small subsurface flaws in complex-shape 3D-printed structures. In contrast, PIT, enhanced by AI, offers a noncontact solution that’s scalable to arbitrary shape and size. This enables manufacturers to check the integrity of 3D-printed metal parts without damaging them during inspection.
This new method could prove especially valuable for industries such as energy and aerospace, where the performance of materials must be guaranteed under harsh conditions. Detecting defects early could prevent costly failures and extend the lifespan of critical components.
Next steps
The researchers are working to refine their technique, aiming to improve PIT’s sensitivity and optimize the AI algorithms for even smaller defects. They also plan to extend the technology to other materials and manufacturing processes.
“This breakthrough shows the potential of AI to solve complex nondestructive evaluation and material science challenges,” said Xin Zhang, postdoctoral researcher at Argonne and coauthor of the study. “By combining advanced imaging techniques with machine learning, we are unlocking new possibilities to ensure the safety and quality of materials used in the most demanding environments.”
The findings highlight a significant advancement in nondestructive evaluation techniques. Engineers now have a powerful tool to assess integrity before materials are put into service.
This work was supported by the U.S. Department of Energy, Office of Nuclear Energy, Nuclear Energy Enabling Technologies, and by the National Nuclear Security Administration.
Kristen Dean is a communications coordinator for nuclear technologies and national security at Argonne National Laboratory.