A Clean Energy Powerhouse: The Digital I&C Systems Modernizing Nuclear
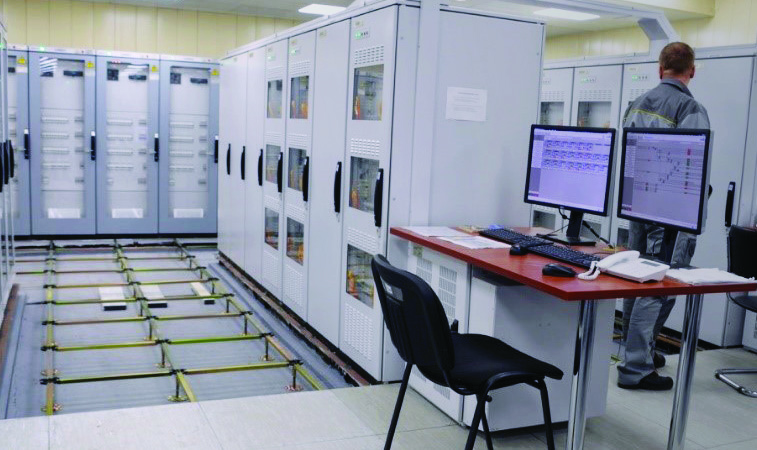
The fight against climate change demands urgent action, and nuclear power—with its proven ability to generate vast amounts of electricity with near-zero carbon emissions—is critical to solving the world’s clean energy dilemma.
Currently, there are more than 440 operational nuclear reactors worldwide, with dozens more under construction and many countries looking to nuclear power for their clean energy future. The global nuclear fleet encompasses a range of reactor designs, from boiling water reactor (BWR) and pressure water reactor (PWR) workhorses to innovative small modular reactors (SMRs).
The key to unlocking this carbon-free powerhouse? Modernizing existing nuclear plants with digital I&C systems.
CROSSING THE DIGITAL DIVIDE
Imagine a nuclear power plant with a highly advanced central nervous system. Digital I&C systems act as this intelligent core. Sensors serve as the system’s eyes and ears, detecting data such as temperature and pressure. Processing units do the brainwork analyzing the data in real-time. A network of cables carries instructions throughout the plant, much like nerves directing muscle movement. Meanwhile, the humanmachine interface acts as the control center, allowing site operators to observe and respond to plant conditions, much like the conscious mind moving the parts of the body.
Digital I&C systems hold the potential to revolutionize the nuclear industry, and yet, widespread adoption of this technology is challenging. Digital instrumentation and control systems perform critical applications where real-time processing, low latency, and high reliability are essential. They must fulfill the specific regulatory requirements of each country, seamlessly integrate with existing plants, and adapt to the design needs of nuclear new build projects.
Consider the following complexities and conditions impacting nuclear I&C as the industry continues moves toward digitalization:
Cybersecurity: As digital technology becomes more prevalent within today’s plants, robust cybersecurity measures are crucial to safeguard against threats and ensure operational integrity.
Advanced Designs: Sophisticated, adaptable I&C systems are needed to manage the unique features of advanced reactors such as SMRs, and Generation IV systems.
Diagnostics: Engineers need integrated diagnostics that can process real-time data to improve predictive maintenance, fault detection, and troubleshooting.
Human-Machine Interfaces (HMI): User-friendly interfaces with advanced visualization tools such as augmented reality (AR) and virtual reality (VR) will play a larger role in aiding plant operators.
Modular and Scalable Systems: Nuclear power plant design is trending towards modular, adaptable systems that can enable easier upgrades, extend the lifespan of existing plants, and accommodate new reactor designs.
Regulation and Collaboration: Regulatory frameworks are adapting to I&C advancements, facilitating international collaboration, standardization, and the exchange of best practices.
A PROVEN PLATFORM FOR I&C MODERNIZATION
As the industry responds to these imminent I&C concerns, a growing number of plants have already adopted the RadICS Digital I&C platform—a flexible, scalable solution with over 100 systems installed to date and successful SIL-3 certification. The RadICS platform leverages Field-Programmable Gate Arrays (FPGAs) and Complex Programmable Logic Devices (CPLDs). This hardware and software diversity eliminates cyber security and common cause failure licensing concerns. The RadICS design also offers other inherent security advantages including:
Flexible architecture that allows the platform to be adapted to implement nearly any kind of I&C system for any reactor type. The platform features a central logic module, alongside various signal receiving and generating modules, and an optical communication module.
I&C functions built directly into the hardware. The RadICS platform operates without the software components often targeted in cyberattacks. Additionally, the hardware design process and reprogramming require physical access, further reducing vulnerabilities and risk. Malware targeting HDL code—the language used to configure FPGAs—is currently non-existent, and the inability to connect standard storage devices eliminates another infection route for control logic.
A DIGITAL I&C SUCCESS STORY: INSTALLATION AT RIVNE NUCLEAR POWER PLANT
Since 2017, the Rivne nuclear power plant in Varash, Ukraine has utilized RadICS digital I&C systems for its plant operations. Rivne selected the platform for the flexibility of its digital architecture, logical design, near-100% diagnostic coverage, channel redundancy, and compliance with the latest nuclear regulatory requirements.
The RadICS platform is designed to be functionally similar to the plant’s previous analog I&C systems, which allowed Rivne to streamline the installation, reengineering, and upgrade process. Rivne now relies on the RadICS platform as the basis for a Conventional Island (CI) Control System, a Nuclear Island (NI) Instrumentation System, and two Engineered Safety Features Actuation Systems (ESFAS).
The new equipment features a smaller footprint and fewer cabinets than the analog equipment it has replaced, while adding significantly more diagnostic and monitoring capabilities. The new modular I&C system is also much simpler with only 10 module types, compared to the 34 module types in the Kaskad-2 I&C (also called UKTS) safety system that it replaced.
THE KEY TO PLANT MODERNIZATION
By replacing outdated analog equipment with digital technologies, nuclear plants can transform plant operations while improving safety, lowering operating costs, and protecting against technology obsolescence. Digital I&C systems are the cornerstone of these plant modernization benefits.
Real-time system diagnostics enable early detection and correction of issues. Self-testing, monitoring, and diagnostic functions allow plants to implement condition-based maintenance, while also simplifying troubleshooting and repairs. Equipment health monitoring and performance indicators minimize the need for manual surveillance activities, reducing the burden on maintenance personnel and increasing plant efficiency. In addition to resolving current obsolescence issues, digital I&C systems are more adaptable than their analog predecessors, offering added protection against future equipment obsolescence issues.
As nuclear power steps into the clean energy limelight, digital I&C systems will be the key to unlocking its full potential.
About the Author
Victor Camacho is the product line manager for digital safety systems at Curtiss-Wright. He has worked with safety and non-safety digital control systems in nuclear power plants and petrochemical distribution centers since 1984.
Curtiss-Wright has partnered with RadICS to bring the RadICS digital I&C platform to the U.S. nuclear fleet. The Curtiss-Wright Digital Safety System (DSS) is an SER approved, credited as digitally diverse, FPGA solution to current digital system licensing bottlenecks and concerns. The DSS is built on the RadICS digital I&C platform, which is robust, flexible, and scalable.
Curtiss-Wright’s Plant Information Monitoring and Control headquarters in Idaho Falls, ID designs, configures, integrates, and tests the RadICS system under Curtiss-Wright’s long standing 10CFR50 Appendix B quality program. Development and test facilities ensure direct and immediate support of plant operations. A full complement of modules and associated materials are maintained in a secure inventory in the Idaho facility. Prospective customers can experience the DSS system at Curtiss-Wright’s Idaho Falls facility via a fully functional 4-division demonstration unit for a reactor protection system (RPS).
To schedule a visit or request more information, visit: cwnuclear.com/DSS