Westinghouse Parts Business Overview, Parts Quality Program
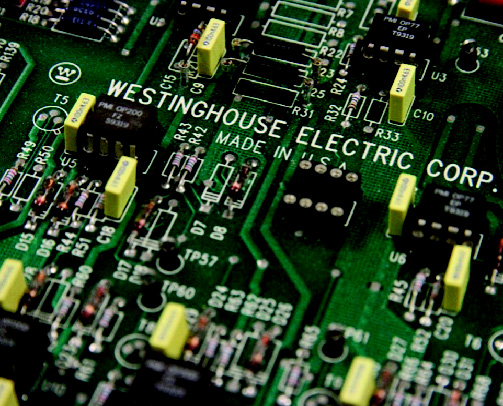
INPO IER 21-4
Safety and reliability have long been hallmarks of the commercial nuclear industry, which has averaged an annual capacity factor over 90% since 2012 and generates more than 775 GWh of clean energy each year (US EIA).
In an industry driven to continuously improve to maintain plant availability at high levels, equipment reliability remains a frequent subject of conversation between nuclear plant operators and suppliers. In September 2021, INPO released event report 21-4 titled “Improving Plant Reliability” and identified a steady trend in equipment-related events which resulted in lost generation of 38 million MWh between 2018 and 2022. These events were generally preventable and led INPO to make several recommendations to the industry, most notably one that challenged the industry to review and establish a “sustainable parts quality process”.
Nuclear plant operators are taking various approaches to what has been labeled as the “Parts Quality Initiative” for both categorization of parts as well as their treatment relative to the potential consequences of failure or degradation. In general, the aim is to provide confidence in the operational function of an item prior to it being placed in service and the most direct approach is through testing and inspection.
INPO IER 21-4 (Continued)
Based on industry feedback, each unit has 1,000 - 2,000 parts identified as being subject to elevated parts quality requirements. These additional requirements can pertain to items regardless of safety classification and create some unique challenges in terms of part identification and treatment due to the focus on the item design function, its failure consequence and how it has been stored, handled or transported prior installation.
Westinghouse has always made quality of parts a priority, and to support nuclear power plants with their Parts Quality Initiative needs, the Westinghouse Parts Quality Program (PQP) has been designed to provide testing services as well as new parts that are supplied to meet the intent of INPO’s IER 21-4 Parts Quality recommendation.
Westinghouse Experience
Westinghouse provides inspection and performance testing for the entire US Nuclear Fleet and 75% of global utilities
Westinghouse is an industry leader in Commercial Grade Dedication (CGD) and nuclear component manufacturing for 100,000+ parts each year
Westinghouse maintains an extensive library of over 4,000 CGD plans, plus original shop orders, manufacturing specifications, and system and component design information dating back to original plant construction
Westinghouse dedicates over 125 experienced engineers and technicians to supporting high-quality parts engineering, inspection and test activities
CGD and PQP Comparisons
On the surface, Commercial Grade Dedication (CGD) and the Parts Quality Initiative seem very similar. Both require identifying the item functions, may utilize testing to meet the program requirements and are benefited by access to design intellectual property. However, there are significant differences in philosophy and application between the two.
CGD is an acceptance process by which a commercial grade item is designated for use as a basic component by providing reasonable assurance that the commercial grade item will perform its intended safety function. There are four acceptance methods which are utilized to verify critical characteristics of the part identified via a failure analysis. EPRI guidance on this process is endorsed by the NRC (with clarifications) in Regulatory Guide 1.164.
In contrast, Parts Quality, as it relates to INPO IER 21-4, can be applied to an item before or after receipt or acceptance by the end user. It applies to items regardless of their safety classification, and ideally will have a graded approach to treatment of the item based on the consequences of failure or degradation of both safety and design function. There is no regulatory requirement for reasonable assurance, rather the aim is to provide confidence that the item will perform its intended design or operational function prior to being placed in service. Most commonly, this is performed tests and inspections related to the item function, however the INPO Parts Quality Information does not stipulate testing as the only acceptable means of part treatment.
Commercial Grade Dedication… | Parts Quality Program… |
An acceptance process that allows a commercial grade item to be used as a basic component | A graded treatment of quality-related activities based on an item’s consequence of failure or degradation |
Applies to safety-related components | May apply regardless of safety classification |
Regulatory requirements and guidance | No regulatory requirements or guidance |
Dedicating entity must provide reasonable assurance the item will perform its safety function | Utility or supplier applies control measures to increase confidence the item will perform its design function prior to being placed in service |
Four acceptance methods | Many applicable control measures with general preference for functional testing |
Does not consider failure modes due to handling, storage or installation | Should consider failure modes or degradation mechanisms that may occur prior to being placed in service |
Both benefit from detailed component design, function and end-use application information |
To date, the industry has taken the general approach to increasing confidence in part function and meeting the intent of INPO’s Parts Quality Recommendation via tests and inspections in an enhanced receipt inspection process where a third-party provider performs the testing scope. In many cases, particularly for highly-engineered items, the OEM owns the design basis, test fixtures, and know-how to properly evaluate the item’s function with accurate results and without damaging or degrading the part in the process.
Of the 1,000 to 2,000 individual parts typical identified as being subject to a site’s Parts Quality Initiative, Westinghouse has delivered approximately 20% of that population (among PWRs). As the OEM for that mechanical, electrical and I&C equipment, Westinghouse is in the best overall position to test those parts which have been in plant inventory or to supply new parts in accordance with Parts Quality Program requirements which evaluate the item’s function, consequences of failure or degradation, and apply the appropriate means to assess the part’s condition accurately and efficiently.
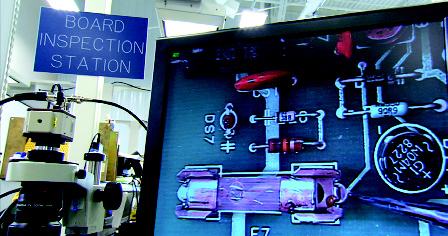
Figure 3 One of several board inspection tools Westinghouse utilizes to produce high quality I&C products
Westinghouse can leverage original nuclear plant system and component design information dating back to original construction, as well as over 4,000 commercial grade dedication plans and experience in the supply of over 100,000 individual items each year to nuclear plants across the globe. The in-house testing and inspection capabilities and expertise of Westinghouse are world class, and in many cases equipment and jigs are specially designed, engineered and constructed to support the delivery of quality components. Whether it is a Westinghouse logic card for your I&C system, a Westinghouse breaker for your 13.8 KV distribution system or a Westinghouse mechanical seal for a critical pump, the 100,000 sq. ft. technical center in New Stanton, PA has the capability to test and supply the part under the Parts Quality Program.
PQP Process
Once a Parts Quality Determination is complete, an assessment is initiated which defines the component, its safety and design functions, and interfacing parts or systems which could potentially contribute to, or be impacted by, failure or degradation of the item.
The next step in the process is to review design information, part and supplier performance history, and other relevant information to establish potential consequences of degradation of failure. In this review, Westinghouse leverages original design information and more than 4,000 CGD plans which contain function, failure mode and critical characteristic information along with test, survey and surveillance results for tens of thousands of parts orders.
Based on the review, a Part Quality Plan is developed to establish appropriate control measures for the part. Tests and inspections are selected to provide confidence in part function without undue risk of damage or degradation which could impact item function once placed in service. Tests and inspections are carried out with the knowledge and experience inherent to the OEM.
Finally, the process needs to be documented. The Westinghouse PQP process leverages existing work procedures, efficient handling and delivery of parts, and a test report is supplied with the item – whether it has been supplied to Westinghouse for functional testing or is a new part delivered under the Westinghouse PQP.
Westinghouse PQP Benefits
Technical Advantages
– System and component design knowledge, specialized test equipment, and experienced resources make sure appropriate tests are performed
Logistics Cost and Schedule Improvements
– The utility typically receives a part, inventories it, ships it to the 3rd party testing facility, receives it back and warehouses it again
– 8+ weeks schedule improvement by choosing Westinghouse PQP parts
Failed Item Returns Costs Eliminated
– Westinghouse handles oversight for failed/returned parts, eliminating cost and burden on the customer
Westinghouse determines appropriate inspections and tests based on item function and application, and supplies a Test Report with the order
![]() Westinghouse Circuit Cards are Designed, Manufactured and Tested by Westinghouse Using State-of-the-Art Methods and Tools | ![]() Westinghouse Maintains a Variety of Specialized Measuring and Test Equipment for Dimensional, Functional and Performance Tests of Components |
Case Study – Parts Quality Initiative List Review
Westinghouse is currently working with various operators to review the items on their Parts Quality Initiative list and determine those items Westinghouse is best suited to test based on status as OEM, experience and specialized testing capabilities. By flagging these items for test or supply through Westinghouse, customers stand to avoid costs and see schedule improvements due to:
• Inadequate or incomplete functional testing of parts for which a third-party does not have design knowledge or test capability
• Damage of parts due to improper or excessive testing
• Damage of parts due to shipping, receiving and handling multiple times between supplier, site and test facility
• Failures and warranty dealt with directly by Westinghouse
• Receiving new parts from Westinghouse which already meet PQP requirements and need no further treatment at customer site
This is a highly recommended first step to allow for sites to optimize value from Westinghouse and simplify the receipt process for parts subject to the site’s Parts Quality Initiative. In addition, once the existing inventory of Parts Quality Initiative items is adequately dealt with, these components can be automatically flagged for supply from Westinghouse under the PQP. The Westinghouse team can perform the necessary evaluation, testing and logistics, which reduces procurement effort by the plant. PQP parts direct from Westinghouse also reduces the burden of oversight on the back end by handling the return of parts and the cost of testing replacements.
Case Study – PQP Control Rod Drive Mechanism (CRDM) Gripper Coil
Among various other components, a customer has identified the stationary gripper coil for their plant’s CRDM as an item subject to their Parts Quality Initiative. When Westinghouse reviewed the plant list of Parts Quality Initiative items, the gripper coil was flagged as a part which Westinghouse would be best suited to test or supply under PQP requirements.
The stationary gripper coil does not have a safety-related function and is continuously energized to hold gripper latches in the control rod drive groove to maintain the control rod in a defined position. When de-energized, the gripper coil allows the control rod to fall by gravity into the core. Intermittent energization of this coil, in conjunction with the other coils in the coil stack, allow for stepping the rod into or out of the core. Although not safety related, function of the part has a direct impact on reactor power. Degradation or failure of the coil has the potential to cause rod position indication errors or changes in reactor power due to unintended rod movement.
Westinghouse maintains the design and quality documentation for this part, including fabrication procedures, instruction manuals, drawings, design limits and test/inspection protocols with acceptance criteria. The coil is subject to various specialized in-process inspections and utilizes materials and construction methods that have been engineered to give the coil a long service life under the demanding environmental conditions present at the top of the reactor vessel closure head. Westinghouse can support customers in functional testing of such a part that they already have in inventory prior to it being placed in service, or by providing a new replacement part that has been assessed in accordance with the Westinghouse PQP. The test and inspections performed will be applied based on the item function, the consequences of its failure or degradation and the history associated with the item.
![]() CRDM Coil Stack Assembly | ![]() CRDM Lift Coil |
PQP Summary
The Westinghouse Parts Quality Program has been developed to meet the intent of the INPO IER 21-4 Parts Quality Recommendation and help our customers with their Parts Quality Initiative goals. Plant operators can expect to see reduced costs and improved schedule when choosing PQP parts direct from Westinghouse by ensuring that the appropriate tests and inspections are performed the first time.
Westinghouse is the best athlete when it comes to testing Westinghouse-delivered parts and can offer genuine Westinghouse components supplied under the requirements of the PQP. Westinghouse’s extensive expertise is not limited to Westinghouse-branded parts, and some example components that Westinghouse can test, inspect and provide under the PQP include:
![]() | Electrical Equipment
|
![]() | Mechanical Equipment
|
![]() | Instrumentation and Control
|
For more information on the PQP program please contact Tyler Upton (uptontr@westinghouse.com) or Matt Cagnetta (matthew.cagnetta@westinghouse.com).
Westinghouse is excited to be working with the industry on solving this issue. For more information on Westinghouse Parts Solutions visit, www.info.westinghousenuclear.com/westinghouse-parts-business.