I&C vendor insights: safety digital technology selection to win the energy market
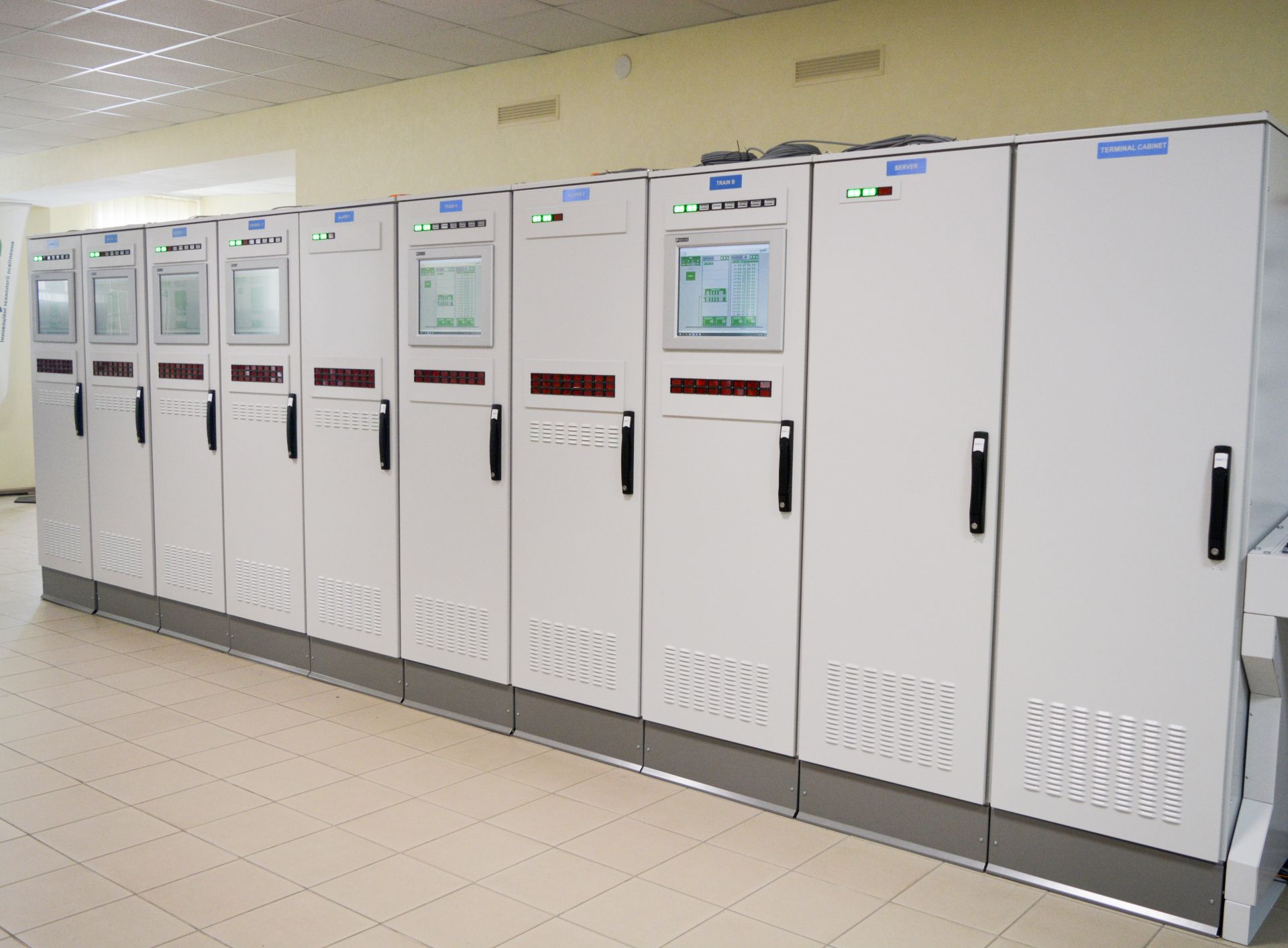
RadICS-based RPS-ESFAS system
Commercial nuclear power plants in the United States (U.S.) face tough competition from sources of alternative generation (e.g., solar, wind, etc.), cheap natural gas, especially in the unregulated market. It is recognized that 35 percent of the U.S. nuclear power plants, representing 22 percent of U.S. nuclear capacity, are at risk of early closure due to economic factors. Plant operators have been reluctant to adopt modern digital technologies for safety-related systems even though these technologies offer many benefits to improve safety and reliability, as well as achieve operating cost reductions.
Significant changes have also been made to improve the U.S. regulatory environment to support the deployment of modern digital technologies through the U.S. Nuclear Regulatory Commission (NRC) digital instrumentation and controls (I&C) Modernization Plans. The changes have sharpened the NRC regulatory review criteria to clearly identify the key safety principles that must be addressed. These improvements were made after a thorough review of lessons learned from recent projects, including the improved review standard used for small modular reactor reviews.
NRC has also improved the processes used to review and approve safety-related I&C modernization projects (i.e., the license amendment review process). The changes were made to address the lessons learned from the reactor protection and engineered safety features actuation system modernization license amendment reviews for several projects, including Duke Energy’s Oconee Nuclear Station and Pacific Gas and Electric’s Diablo Canyon Power Plant modernization projects.
These recent developments in the industry may open the door for plant operators to adopt modern digital technologies for safety-related systems to address I&C obsolescence and to improve their competitive position. Previous obsolescence management strategies to keep analog safety-related I&C viable as long as possible prevented plant operators from reaping the benefits of modern digital technologies. Plant operators now have the choice to address I&C obsolescence, improve overall plant safety and reliability, and decrease the levelized cost of electricity. There is now a path forward for the operating nuclear fleet to maintain the emission free, always-available electricity as an integral part of the future energy mix.
Plant owners now have to understand how to choose from the many I&C vendors and excellent technologies available in the nuclear market. The choice can be daunting, complicated, and time consuming. Radics LLC, an international nuclear engineering company, develops and supplies advanced customized I&C solutions. Their experience in addressing obsolescence through digital I&C upgrades in Europe, Canada, and Brazil tells us that the choice involves more than just initial cost. Radics LLC has found four additional factors to consider in selecting safety-related I&C equipment.
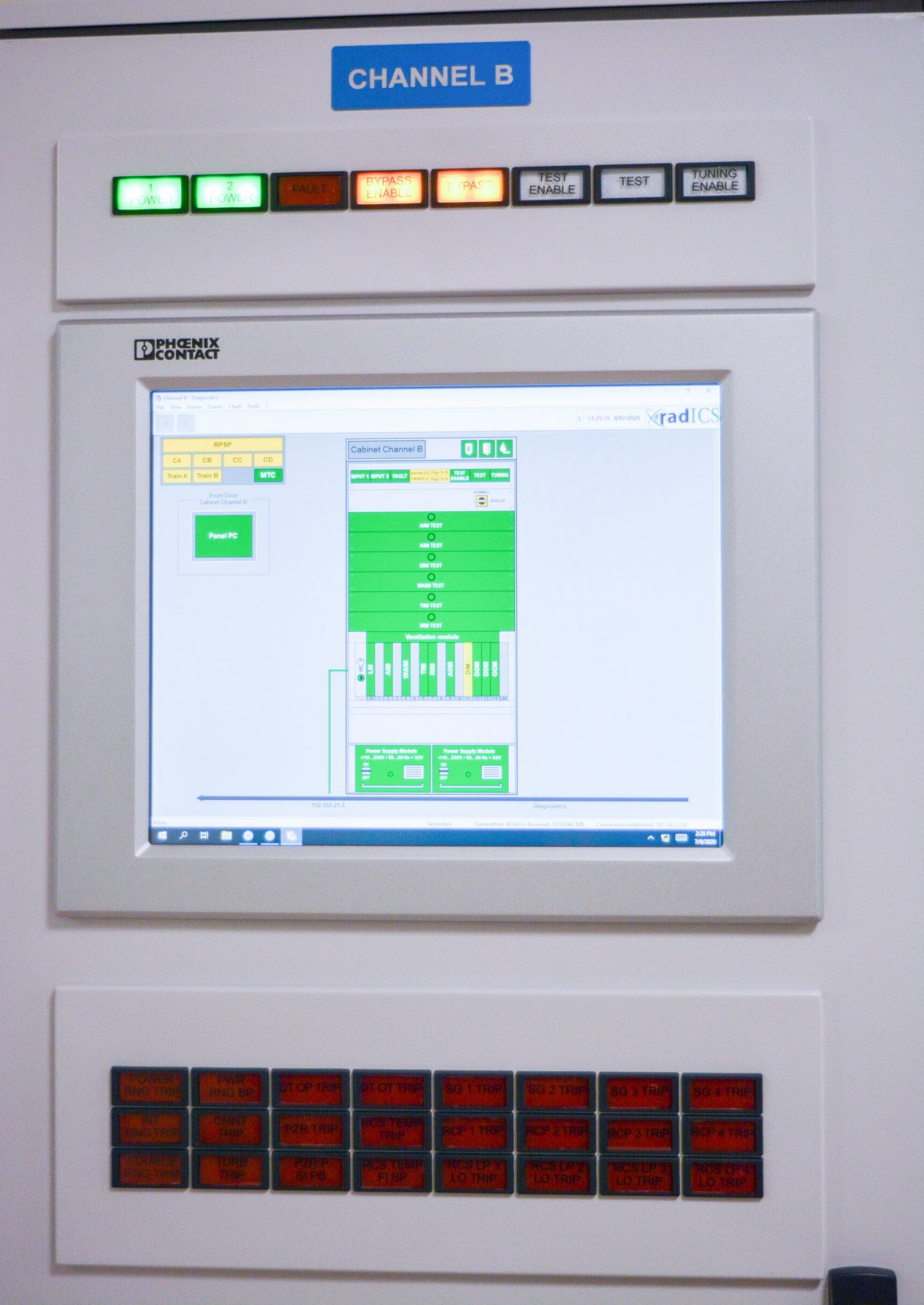
Operator-friendly visualization of diagnostic and process information (typical HMI)
I&C Technology Superiority – It is essential to have clear criteria to differentiate between I&C technologies. Obvious factors often considered include the status of NRC approvals and technical requirements related to input and output device interfaces. It is important to understand the age of the NRC approval and the implementation conditions placed on the technology. It is also necessary to understand what is possible for the upgrade to define additional functionality that provides improvements to safety, reliability, availability, maintainability, and cost of operation.
Best Value with High Impact Return – It is important to look beyond ease of licensing when selecting I&C technologies and developing an I&C system solution. In order to achieve targeted benefits, other factors that should be considered include:
Reduced hardware board count and inventory requirements with improved protection system reliability with higher functionality digital modules
Improved plant safety with higher availability for new system with the use of graceful degradation response to faults detected by self-testing
Used self-testing features to eliminate manual channel functional tests required each calendar quarter
Used self-monitoring features and alarms to automate manual channel checks each shift
Digital diagnostic messaging and module human-machine interface design to simplify troubleshooting and corrective maintenance
Automated end-to-end testing to reduce time and resources required to perform testing during refueling outages
Optimized architecture within cabinet footprint constraints
Redundant voters to improve availability
Vendor Experience – It is always about experience, readiness to deal with known project challenges, and the ability to address unexpected problems that can arise during large project implementation. It is important to consider all experience, not just nuclear experience, because it is valuable for a vendor to have familiarity with a variety of nuclear plant digital I&C projects. It is also important to understand the supplier’s history of product support and product migration. Past performance is an indication of future performance
Enabling Total Nuclear Plant Transformation – The safety-related digital I&C technology needs to support the plant digital transformation strategy and fit into plant work process and workforce plans. If this is not done, the full potential of the digital modernization will not be achieved.
Radics LLC develops I&C solutions based on the innovative RadICS platform, which is a Technically Superior technology. It uses state-of-the-art Field Programmable Gate Array (FPGA) technology, was developed to the most demanding industry standard for safety-critical systems (i.e., IEC 61508) and provides high-reliability at Safety Integrity Level 3. The FPGA technology provides fast and deterministic performance with response times for I&C functions as fast as 5 milliseconds. The reduced operating complexity of the FPGA technology, coupled with the comprehensive self-diagnostics, ensures fail-safe performance through the elimination of systematic faults that cannot be eliminated from microprocessor technologies.
The NRC approved the RadICS platform as meeting or exceeding its regulatory requirements for digital I&C development. Radics LLC was also able to demonstrate that the IEC 61508 design features and internal diversity used to eliminate systematic faults were sufficient to address NRC concerns with digital common cause failure vulnerabilities.
The RadICS Platform provides the Best Value for High Impact Returns. The RadICS technology uses extensive on-line self-testing and comprehensive diagnostics at the module, chassis, and system levels. These features can be used to streamline required surveillance activities and reduce burdens on plant personnel, allowing them to focus on other mission-critical activities. These self-diagnostic features can be supplemented with additional engineered test features for a plant retrofit project to achieve greater automation of required testing to provide further benefits.
The RadlCS Platform creates a new paradigm for addressing common cause failure vulnerabilities. The old paradigm relies on the addition of a separate diverse actuation system to address the common cause failure vulnerabilities associated with microprocessor-based systems. The old paradigm adds system complexity along with increased costs and longer schedules for protection system modernization projects. The RadICS Platform incorporates a unique diversity strategy to address the common cause failure vulnerabilities that does not require a separate diverse actuation system to address the common cause failure vulnerabilities. This unique capability eliminates system complexity along with the reduced cost and implementation resources.
Radics LLC has extensive Vendor Experience with the RadICS Platform. The RadICS technology has been installed worldwide in more than seventy nuclear plant safety and control applications—most of them safety significant, such as Reactor Protection and Engineered Safety Features Actuation Systems. This experience has been coupled with the experience of the Curtiss-Wright Nuclear Division through a strategic partnership to deploy RadICS-based I&C systems to the U.S. market. Curtiss-Wright has experience and proven mitigation approaches on large-scale I&C modernization projects to deal with digital I&C modernization project challenges.
RadICS technology can Enable Total Nuclear Plant Transformation. The technology can support interfaces with other digital technology at the plant to support overall efforts for plant digitalization, migration to data-driven maintenance and, business process optimization. The RadICS technical features can simplify maintenance, troubleshooting, and surveillance testing, and can support operator “mind digitalization” and culture change. Those are important factors for a company’s ability to attract and retain new, younger workers.
It is important that nuclear plants continue to provide safe, carbon-free, and reliable sources of electricity. Movement towards I&C modernization will allow plant owners to increase safety and reliability while also reducing operating costs, important considerations in today’s competitive energy market. The move to digital can be intimidating but by taking a wide-angle approach and focusing on factors beyond initial cost, today’s nuclear plants can set the stage for a promising future.