TRU Waste Solution inDRUM Treatment
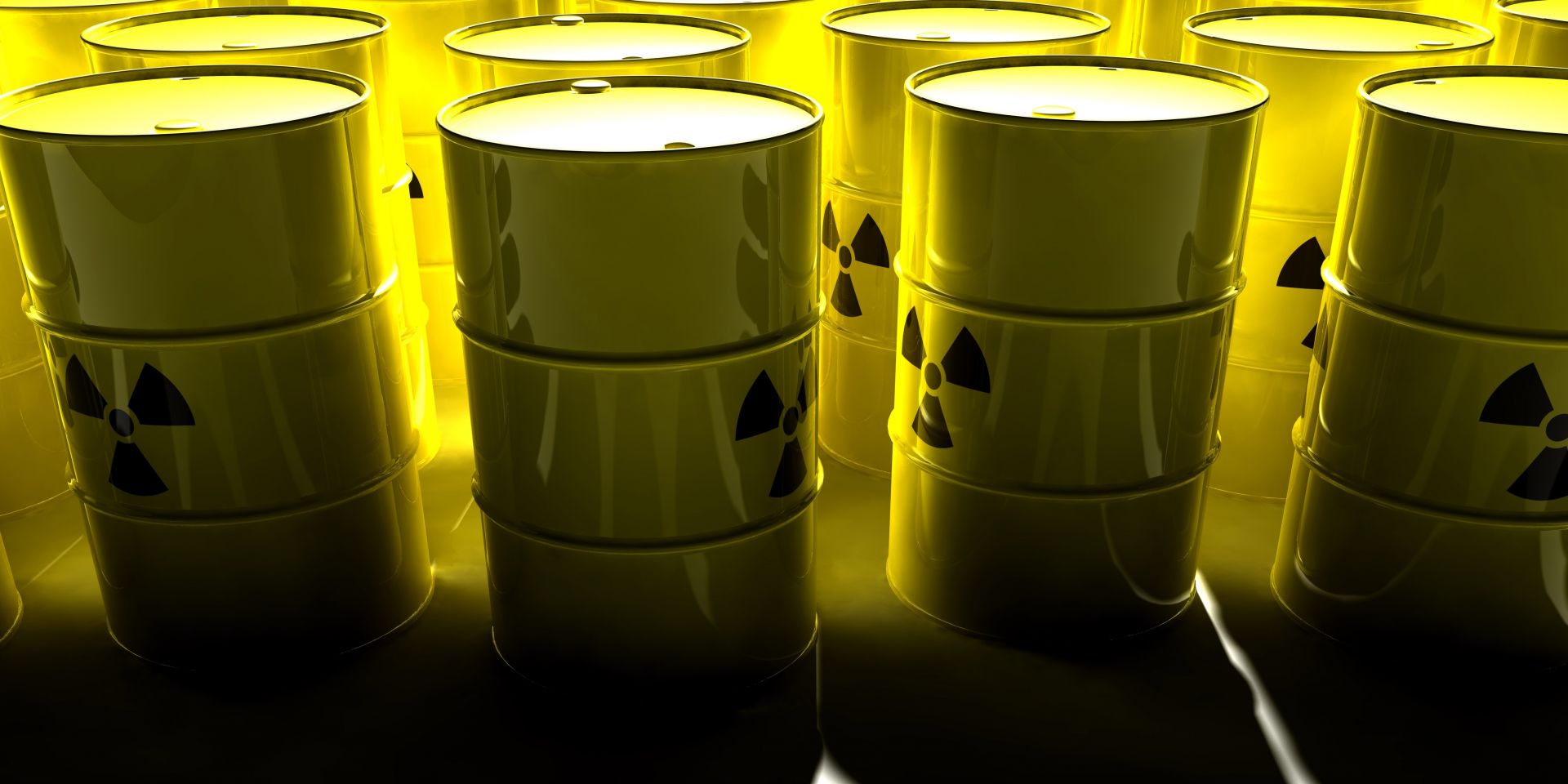
Do you have TRU waste with characteristics and/or prohibited items not acceptable in their current configuration for transportation and/or disposal at WIPP? Such as liquids, oxidizers, corrosives, reactive materials, flammable liquids, and aerosol cans? Are you sorting and segregating the non-compliant waste forms and then developing process/treatment approaches (i.e., solidification, grouting, deactivation, etc.) to ensure your final waste form will meet transportation and WIPP’s acceptance requirements?
Studsvik’s has a patented inDRUM solution designed specifically to remedy this situation.
inDRUM is a batch thermo-chemical system that treats containerized radioactive wastes by means of in-container thermal treatment to remove the free liquids, destroy organics, and deactivate corrosives and reactive materials from the containers. Treatment is achieved without removing or handling/sorting wastes from the container. In most applications, wastes are treated in the container in which the wastes were originally packaged. The thermally decomposed waste form is an inert, inorganic dry char (ash-like substance), significantly volume reduced (as much as 90%). The inDRUM process:
- Removes unwanted liquids via evaporation and/or thermal decomposition;
- Neutralizes or deactivates reactive materials, corrosive chemicals and pyrophoric metals converting them to non-hazardous oxides or carbonate compounds;
- Thermally decomposes nitrates into gaseous NOX;
- Evaporates or pyrolytically gasify organics including plastics;
- Removes unwanted contaminants or coatings from inert materials (such as concrete, sheet rock, metals, etc.);
- Safely breaches sealed containers, such as aerosol, paint cans, jars and scintillation vials resulting in the waste types contained in these various configurations to be properly treated; and
- Provides a robust design making it possible to treat poorly characterized wastes by thermally removing/destroying all non-compliant characteristics.
The Figure 1 provides a summary of the key benefits of the inDRUM treatment solution. These benefits are further described in this document following the figure.
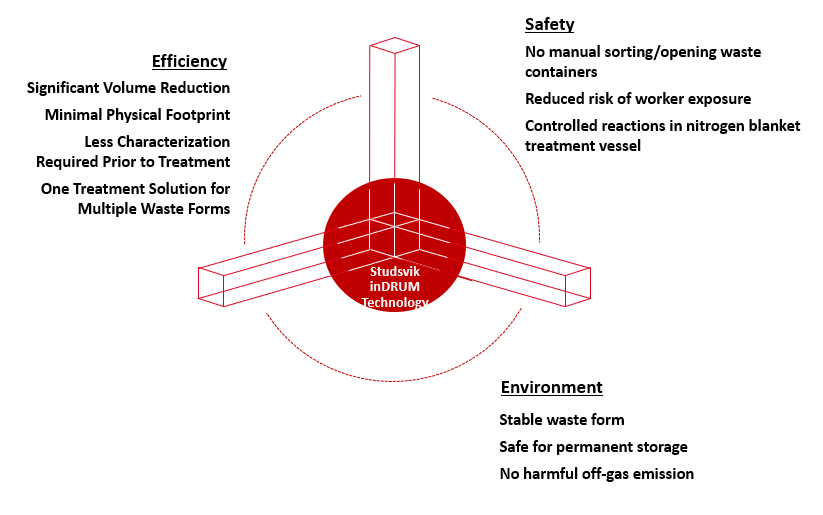
Figure 1 - Customer Values provided by Studsvik inDRUM Treatment Solution
Stable Waste Form: inDRUM guarantees that product residues remain in the treated drum and consist of dry, inert, inorganic waste material and inorganic carbon char. This stable waste is a more homogenous waste form providing efficient sampling to ensure the final analytical results are representative of the entire container content. This removes risks of mischaracterization inconsistencies. The inert waste form also removes risk of an energetic chemical reaction involving TRU wastes.
Worker and Environmental Safety: Treatment is achieved without opening the TRU container due to the wide range of waste types that can be processed. Additionally, the system is conservatively designed to minimize the sampling and characterization of waste that is required. These unique attributes reduce/prevent worker exposure to radiation or hazardous organics and gases, the spread of contamination (especially alpha contamination), the chance of a spill or airborne release, etc.
No Harmful Emissions: inDRUM applies a nitrogen blanket and indirect heating of the TRU waste at low temperatures, mitigating concerns of radioactive volatility. Using a sophisticated, proven, control of the thermal process, escape of particulates from the waste container is minimized. In addition, a sophisticated barrier filter system is employed to capture any particulates that may escape the container, resulting in a particulate-free gas sent to the off-gas system.
Volume Reduction: inDRUM will reduce the actual TRU waste volume up to a factor of 10 (resultant waste is 1/10th initial volume). If the TRU waste is loaded into the system using 55 gallon/200 liter steel drums, the limiting factor in terms of volume reduction is how much the steel drum can be compacted. Typical industrial super compactors can be employed which compact the steel drums by a factor of 6. These volume reductions directly, reduce costs, proportionally associated with treating TRU Waste (e.g. packaging, storage, shipping and disposal costs).
Processing Flexibility: inDRUM has a small physical footprint designed to be deployed directly onsite. Flexibility in the design allows for a range of configurations, suited to client’s specific needs, from a single processing unit, capable of processing 50 m3 of TRU waste annually, expandable to processing up to 200 m3 annually. The equipment is designed for a life expectancy of 20 years of operation.
The inDRUM technology can be used on radioactive wastes including Low-Level, Intermediate and High-level Waste. Table 1 below provides a list of waste types that have been tested and proven to be acceptable for processing through the system.
Table 1 - Additional Waste Types That Can Be Treated Using Studsvik’s inDRUM Technology
Absorbent wipes | Dried paint chips | Masking tape | Rubber |
Acids | Dust/Ash | Mercury | Rubber hoses |
Aerosol cans | Fe OO H | Nitrates | Sealed cans |
Air filters | Filter cartridges | Nitrites Oil | Scintillation vials |
Al (OH)3 | Flammable liquids | Oxidizers | Sludge |
Bottled liquids | Fluorescent powder | Paper | Sludges with reactive metal |
Calcium fluoride slags | Fly ash | Paper towels | Sulfonated compounds |
Caustics and Bases | Free liquids | Polyethene PVC | Water |
Cellulose | Hydrocarbons | PVC suits | |
Chlorinated compounds | Iodine | Reactive metals | |
Corrosives | Latex shoe covers | Resins |
inDRUM Solution vs. Alternative TRU Treatment Options: Other treatment options require the removal of prohibited items (i.e., aerosol cans) and/or changing waste characteristics by manual or remote sorting and repackaging. These efforts are costly, time-consuming, increase worker radiation exposure, increase the risk of spread of contamination and airborne releases, and can create secondary waste streams that require additional treatment. The inDRUM addresses these concerns by safely and effectively treating waste without removing the waste from the original containers. For each site to develop an individual path forward for the processing of TRU wastes takes significant time. The inDRUM solution provides one solution for TRU difficult waste types removing these onerous and costly steps for each site to develop a compliant path forward.
Next Steps: Studsvik can review your TRU waste volumes and provide a recommendation on how best to apply the inDRUM treatment solution to remediate volumes while minimizing cost.
For further information please contact:
Tammy Monday
Vice President Business Development and Sales
Studsvik, Inc.
Tel: 865-599-9605
Email: tammy.monday@studsvik.com
www.studsvik.com
inDRUM Process – Additional Technical Overview
The inDRUM process consists of two main treatment systems: the Container Treatment Vessel (CTV), where thermal treatment of drums is performed, followed by an off-gas treatment system that oxidizes any Volatile Organic Compounds (VOC), carbon monoxide, and traces of hydrogen volatized from the CTV and removes and/or neutralizes any acid gases, mercury or iodine present in the off-gas stream.
The CTV is fabricated of a high-temperature, corrosion-resistant alloy suitable for contact with the organic gases, steam, and acid gases that are volatized from the waste inside the container during thermal treatment. The CTV is electrically heated using externally mounted, ceramic-insulated, electrical heating elements that provide the energy to heat the CTV and container with waste materials inside to the necessary evaporation and organic decomposition temperatures.
Containers of contaminated waste are gradually heated inside of the nitrogen and/or steam blanketed CTV. This results in significant volume reduction and conversion of the original waste materials as the waste inside the container is heated at a controlled heating rate.
As the waste inside the drum heats up, any water in the container will evaporate, organics will evaporate or thermally decompose to form low molecular weight VOC vapors, and corrosives (acids and bases), oxidizers and reactive materials are converted into non-hazardous oxides or carbonate compounds.
Applying steam to the residues in the treated container gasifies the carbon in the residues into carbon monoxide and carbon dioxide (CO2) along with the release of traces of hydrogen further reducing the final volume of the treated residues. Once the process is complete, the CTV and waste container are cooled using a nitrogen gas atomized water spray. The atomized water mist rapidly evaporates into steam in the CTV.
At the end of the cooling cycle, the partially cooled container with inorganic residues inside is then removed from the CTV and transferred to a holdup area where the container cools to near ambient temperatures.
The steel waste drums will retain their initial integrity as the inDRUM treatment process will only result in the paint on the drum being pyrolyzed and a thin oxide film (rust) that will form on the inside and outside surfaces of the carbon steel drums. If an incoming waste drum is not structurally sound, the waste drum will be placed inside a larger overpack drum, such as a 320L (85 gal) drum, which will be undamaged by the treatment process.
inDRUM uses readily available consumables, for example, electricity for heating, demineralized water, and nitrogen gas. The equipment is designed for a life expectancy of 20 years of operation.