Organic Cooled Reactors: Five Fast Facts!
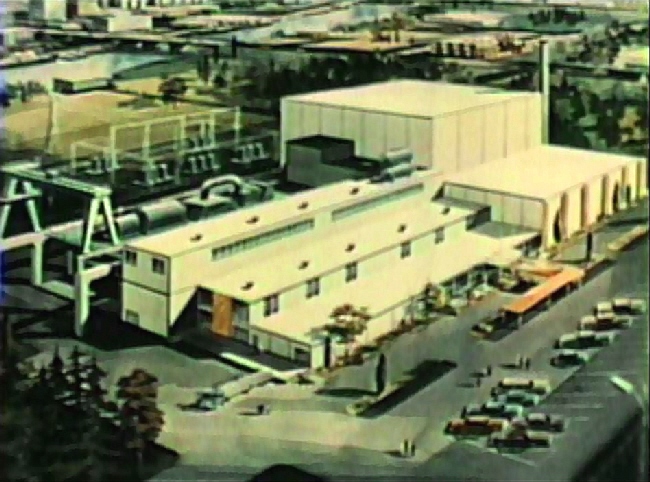
Early 1960's artist's concept for a commercial organic cooled nuclear power plant - right near a city. This isn't far from what actually happened as we'll see below. Concept art published by Atomics International.
The present re-examination of reactor principles tried in the past but for one or another reason sidelined has skipped a very significant principle: Organic coolant. This was an early idea which received a great deal of research and press during the great buildup of nuclear technology; today, it's largely been forgotten. Let's take another look!
1. Organic coolant was conceived early. According to E. F. Weisner of Atomics International (1) the idea of using a hydrocarbon fluid as either coolant, or coolant and moderator, in a nuclear reactor goes all the way back to the Manhattan Project of the Second World War years. While gas cooling (with graphite moderator) and water cooling (with water moderator) took over the lead of power reactor development after the end of the Second World War, an important meeting was held in August 1953 in Downey, California during which engineers first undertook serious consideration of hydrocarbon fluids for use in power reactors. Thus, the serious consideration of organic coolant (and moderator) dates from just about the time that pressurized water plants proved workable.
2. Organic coolant means great qualities. Because the kinds of organic materials (2) used for early reactors had low vapor pressures, the plants they would be used in could be designed to operate at very low system pressures. This removed a lot of the consideration about pressurized release of coolant and energy if there was a leak. Also, they could be operated at fairly high temperatures. This combination of features meant that organic cooled plants could provide superheated steam (since the coolant could operate safely up to about 700F), and do it without the extremely heavy and expensive kind of primary system called for in light water reactors. Today, such plants, if built, could be used to replace fossil powered boilers since organic cooled reactors can provide the steam quality needed for a direct replacement.
3. Organic coolant means less expensive plants. Because the materials used in much of the primary coolant system of an organic cooled plant are more of the quality found in petrochemical or petroleum handling plants than nuclear plants, the cost of the components is significantly reduced. Further, because organic coolant doesn't corrode metals there's no need for expensive plating of surfaces to prevent corrosion. There is a cost associated with the coolant use, because organic coolant undergoes both pyrolitic (temperature related) breakdown as well as radiolytic (radiation related) breakdown, so that more coolant has to be added constantly by feed-and-bleed. However, this is a supply (operating cost) problem of only small magnitude and not a construction cost problem.
4. Organic cooled plants were both prototyped and built commercially! Two major experiments were carried out concerning organic cooled reactors; the Organic Moderated Reactor Experiment at NRTS, Idaho Falls (now INL) and the Piqua Nuclear Power Facility in Piqua, Ohio.
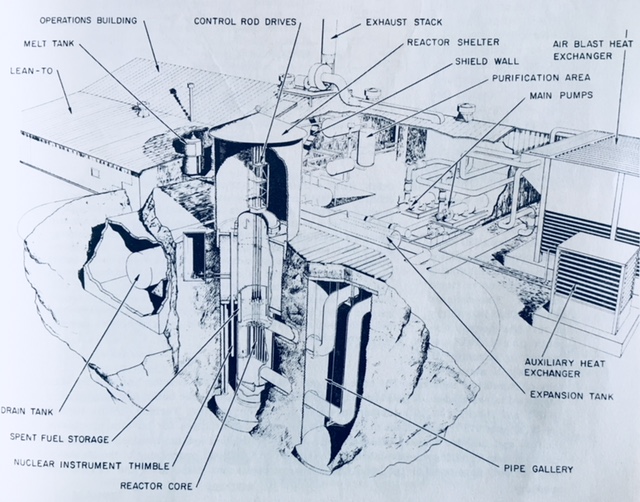
The Organic Moderated Reactor Experiment was a project jointly built by the AEC and by Atomics International in 1956-1957. It first operated in September 1957 and reached its full design power of 12 MWt in February 1958. The plant had no generating equipment, but dispersed heat through use of an air blast heat exchanger. Structures were weather shelter only; the plant had no containment as we'd think of one today. Illustration from "Experimental Power and Test Reactors," US AEC 1956.
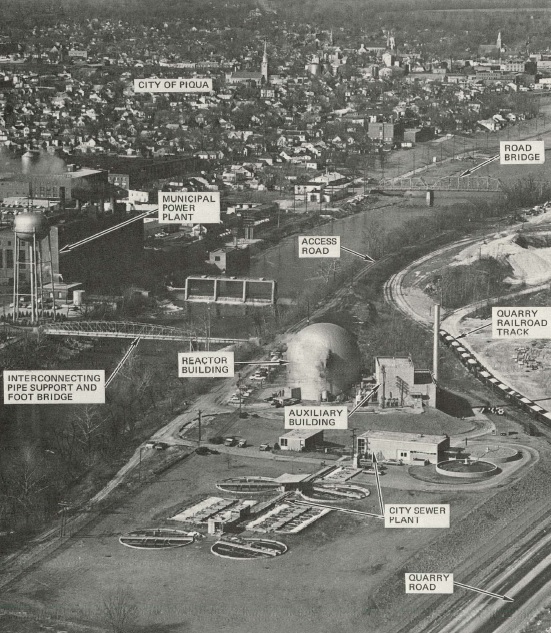
As you can see, not only was a commercial nuclear power plant built using organic coolant but it was built right near the city of Piqua, Ohio! The plant fed steam over to the original municipal power station. The plant was a project of the AEC, the City of Piqua and Atomics International. Initial startup was in June, 1963 with operations continuing until January 1966. At that time a large deposit of solidified material was discovered in the core; complete cleanup of the material, caused by oxidation of cracked coolant (itself a result of too low a coolant velocity in the moderator section of the fuel elements) was completed and total redesign of the core also completed to nullify this effect when the AEC decided to defund all organic coolant research in late 1967. Much of the plant was dismantled but the reactor vessel and primary system were entombed in the enclosure, which itself was otherwise fully released for use and today is used by the city for storage. Photo from "Retirement of the Piqua Nuclear Power Facility," Atomic International 1970.
5. The next steps for organic cooled reactors are clear. While some other varieties of advanced reactor concepts were left with more questions than answers, the next steps for organic cooled reactors were made pretty clear in the volumes of material created during the program. For example, the Piqua reactor had serious problems later on with coolant cracking down to "high boilers," then polymerizing and jamming up channels. This was found to be a simple flow control problem which kept some coolant too hot for too long. Another problem with organic cooled reactors is that they required enriched fuel if they were to use organic material as both coolant and moderator - but Atomics International already got around that by planning to use heavy water as a moderator in larger reactors. In fact, they designed, at least conceptually, organic cooled and heavy water moderated reactors up to around 8000 MWt for the AEC. Use of heavy water as the moderator also greatly reduces the daily makeup requirement of fresh organic material. Yes, there's already a clear road map for "next steps" in organic cooled reactors.
Two fast footnotes....
(1) This information is found in the remarkable "Solid Fuel Reactors," published by the AEC in 1958. The section on organic cooled reactors was written by Weisner, who we might well guess was present at the 1953 meeting that probably put North American Aviation on the path to organic coolants. (North American later split off its nuclear activities into a wholly owned company, Atomics International - but that hadn't been formed yet in 1953.)
(2) So what are organic coolants, anyway? Well, they're "aromatic" hydrocarbons that are somewhat waxy and can be pumped like oil. They were used as pumpable thermal insulators in some kinds of processing plants. They have a low specific heat capacity, but their qualities as mentioned in the article above make this factor far less important. Monsanto Corporation sold a variety of off the shelf terphenyl mixtures that were used at times in organic cooled reactors and/or experiments under its Santowax brand name. The Atomic Energy Deskbook (Hogerton, 1963) describes such materials as "benzene derivatives." The author can provide more information to those interested.
Please feel free to leave a constructive comment below!
Will Davis is a member of the Board of Directors for the N/S Savannah Association, Inc. He has been a contributing author for Fuel Cycle Week, and he used to write his own popular blog Atomic Power Review. Davis is also a consultant and writer for the American Nuclear Society, and serves on the ANS Communications Committee and the Book Publishing Committee. He is a former U.S. Navy reactor operator and served on SSBN-641, USS Simon Bolivar. His popular Twitter account, @atomicnews is mostly devoted to nuclear energy. He has an Instagram at @williamdavis5500, but that's mostly dog photos.