New GE Hitachi “blocks” could cut costs in nuclear deployment
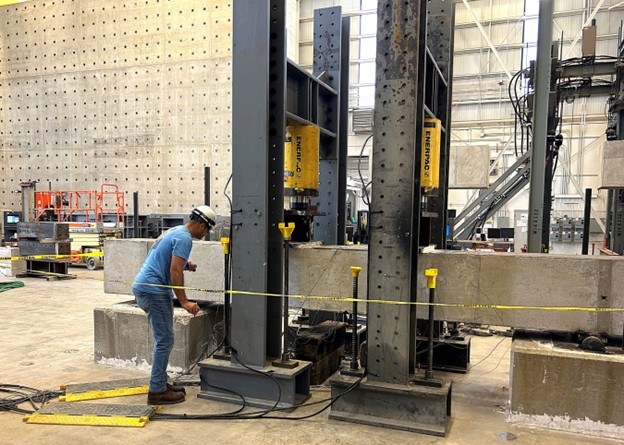
Researchers at GE Hitachi Nuclear recently completed a successful test on potential new building blocks made of steel-concrete composite.
In partnership with the U.S. Department of Energy, GE Hitachi is looking for innovative building materials aimed at reducing nuclear construction costs by as much as 10 percent. The diaphragm plate steel composite (DPSC) specimens “exceeded our expectations,” said Luke Voss, program manager at Idaho National Laboratory, in a press release issued today by the DOE’s Office of Nuclear Energy.
“We are very excited and enthusiastic about the use of this construction technology to help save time and money in the deployment of new nuclear reactors,” he added. INL is a partner in the project.
Testing process: Researchers filled the DPSC specimens with concrete to simulate a reactor containment wall. They were then subjected to various loading conditions to mimic real-life situations, like an earthquake, that a containment building might experience.
The success of the small-scale demonstration, conducted at Purdue University’s Bowen Laboratory in Indiana, cleared the way for the technology to be used in future demonstration projects.
The DOE’s National Reactor Innovation Center (NRIC) is reviewing a GE Hitachi proposal to build part of a reactor containment building using the DPSC design to further test the technology. If approved, that demonstration would also test digital twin technologies on the civil structure and techniques that were developed in the original phase of the project.
Elsewhere, GE Hitachi plans to use the DPSC technique for its first four BWXR-300 small modular reactors in Ontario, Canada.
Building better blocks: The team behind the DPSC design said it has advantages over the traditional steel-concrete composite.
It provides reinforced concrete with two continuous steel plates connected using adjoining plates with circular concrete flow holes. Also, the steel wall modules can be fabricated and shipped anywhere, assembled on-site, and then filled with concrete, resulting in a quicker construction timeline and lower labor costs—both common criticisms of the U.S. nuclear industry.
Once on-site, the modules can be welded together end-to-end or stacked vertically to allow for design flexibility, faster quality control inspections, and even substitution of some of the plate materials during the manufacturing process to meet nuclear plant corrosion requirements.
Quotable: “The successful design, fabrication, and testing of DPSC modules demonstrates the potential of this advanced fabrication and construction technology to lead to cost savings and improved project schedules in the deployment of small modular reactors,” said Sean Sexstone, executive vice president of advanced nuclear at GE Hitachi.