Optimizing Maintenance Strategies in Power Generation: Embracing Predictive and Preventive Approaches
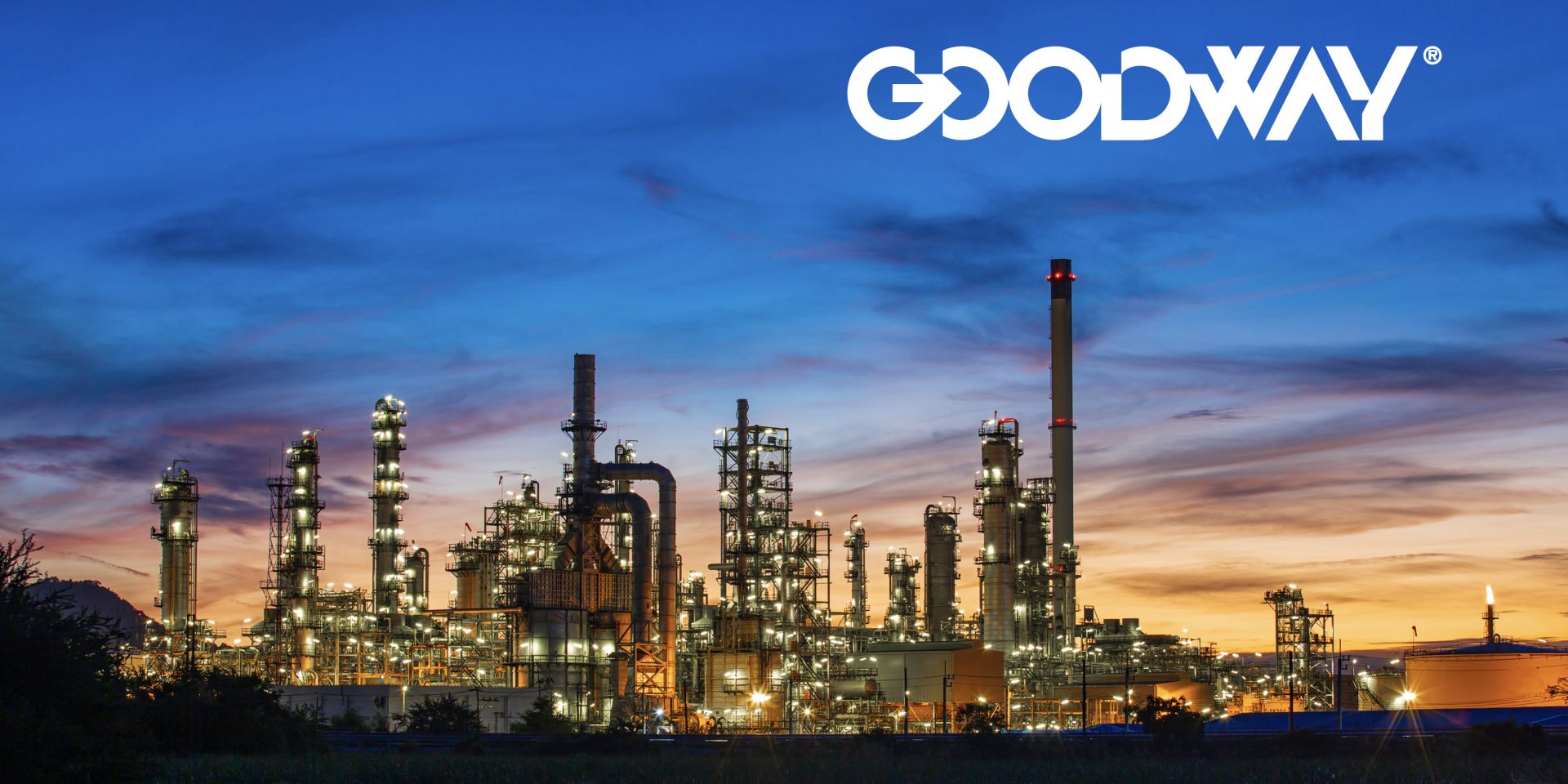
In the high-stakes world of power generation, ensuring continuous operation and reducing downtime are central priorities. With the increasing complexity of power generation systems, maintenance practices are evolving to meet these demands more efficiently. Understanding the roles of Predictive Maintenance (PdM), Preventive Maintenance (PM), and Reactive Maintenance (Run-to-Failure) is crucial for maintenance professionals in the energy sector to make informed decisions about equipment management and long-term operational strategy.
Predictive Maintenance: Proactively Preventing Failures
Predictive maintenance (PdM) is revolutionizing equipment reliability in power generation facilities. By leveraging data analytics, sensors, and machine learning, PdM continuously monitors asset conditions, predicting failures before they occur. This proactive approach is particularly critical in industries like nuclear power, where avoiding failures is paramount. PdM allows operators to act before a breakdown disrupts operations, minimizing unplanned outages.
The main advantage of PdM is its ability to detect issues early, enabling facilities to schedule repairs only when necessary. This prevents catastrophic failures, reduces unnecessary maintenance, and generates long-term cost savings. Predictive tools also help manage equipment wear, extending machinery life and avoiding costly emergency repairs.
Additionally, PdM enhances safety by forecasting potential failures, reducing the risk of hazardous breakdowns that could endanger personnel. By integrating predictive maintenance into daily operations, energy facilities can reduce downtime, improve asset longevity, and maintain a safer work environment.
Preventive Maintenance: A Scheduled Approach to Reliability
Preventive maintenance (PM) is fundamental for ensuring equipment reliability with moderate risk or regular maintenance needs. PM involves scheduled maintenance at fixed intervals, regardless of equipment condition, which helps maintain optimal performance and significantly reduces the chance of unexpected failures.
Regular inspections, lubrication, and part replacements under PM plans extend the lifespan of key components and improve efficiency. While less advanced than PdM, PM is cost-effective and simpler to implement, making it ideal for essential, non-mission-critical assets. PM saves money over reactive maintenance by preventing breakdowns and reducing the risk of costly repairs due to neglect.
In power generation plants, PM ensures the reliability of turbines, boilers, generators, and HVAC systems. Routine checks identify minor issues before they escalate, boosting equipment reliability and enhancing safety. Though it doesn’t require predictive tools, its structured approach keeps critical systems running smoothly.
Reactive Maintenance: The High Cost of Running to Failure
Reactive or run-to-failure maintenance involves letting equipment operate until it breaks down, followed by corrective repairs. While this approach may seem cost-effective in the short term, it leads to higher long-term expenses, as emergency repairs, parts replacements, and downtime are far more costly than planned maintenance.
Reactive maintenance risks operational efficiency in power generation facilities. Unexpected breakdowns can halt production, causing financial losses and disruptions. Running equipment to failure accelerates wear, reducing asset lifespan and increasing repair costs.
Furthermore, reactive maintenance poses serious safety risks. Sudden failures can lead to dangerous accidents, especially in high-pressure or high-temperature systems. For this reason, run-to-failure maintenance is best reserved for non-critical, low-cost assets where failure won’t significantly impact operations.
Which Strategy is Best for Power Generation Facilities?
Each maintenance strategy has its place in the power generation sector. Predictive maintenance is best suited for high-value, mission-critical equipment where uptime is essential, such as turbines, generators, and boilers. By predicting failures before they occur, PdM optimizes maintenance schedules, minimizes downtime, and extends equipment life—ensuring continuous power generation without interruptions.
Preventive maintenance is ideal for assets that require regular servicing and where the risk of sudden failure is moderate. It’s a reliable, cost-effective approach that maintains the efficiency and reliability of important equipment, contributing to overall operational success.
While occasionally necessary, reactive maintenance should be reserved for low-risk, low-cost assets where the impact of a failure is minimal. Given the significant drawbacks regarding downtime, repair costs, and safety concerns, relying on reactive maintenance as a primary strategy in critical areas of a power generation facility is not advisable.
Conclusion: A Modern, Integrated Approach to Maintenance
The key to optimal maintenance in power generation facilities lies in choosing the right strategy for the right equipment. While predictive and preventive maintenance offers proactive solutions for maintaining reliability, safety, and cost-effectiveness, reactive maintenance should be used sparingly and only when necessary.
Integrating predictive and preventive maintenance practices into everyday operations offers significant advantages for modern power generation facilities that want to remain competitive.
Goodway Technologies is a provides a robust offering of preventive maintenance equipment including ScaleBreak® descaling chemicals, clean-in-place pump systems, rotary tube cleaners, surface condenser cleaning systems, industrial vacuums and much more. Our equipment is engineered to be easy to operate, efficient, and highly effective to reduce downtime and labor costs. Plus, our sales engineers can provide consultation to ensure you get the right solution to meet your maintenance needs. Check out all our power plant cleaning and maintenance equipment.