Transport by Barge and Road: Shipping Crystal River’s Segmented RPV to Disposal
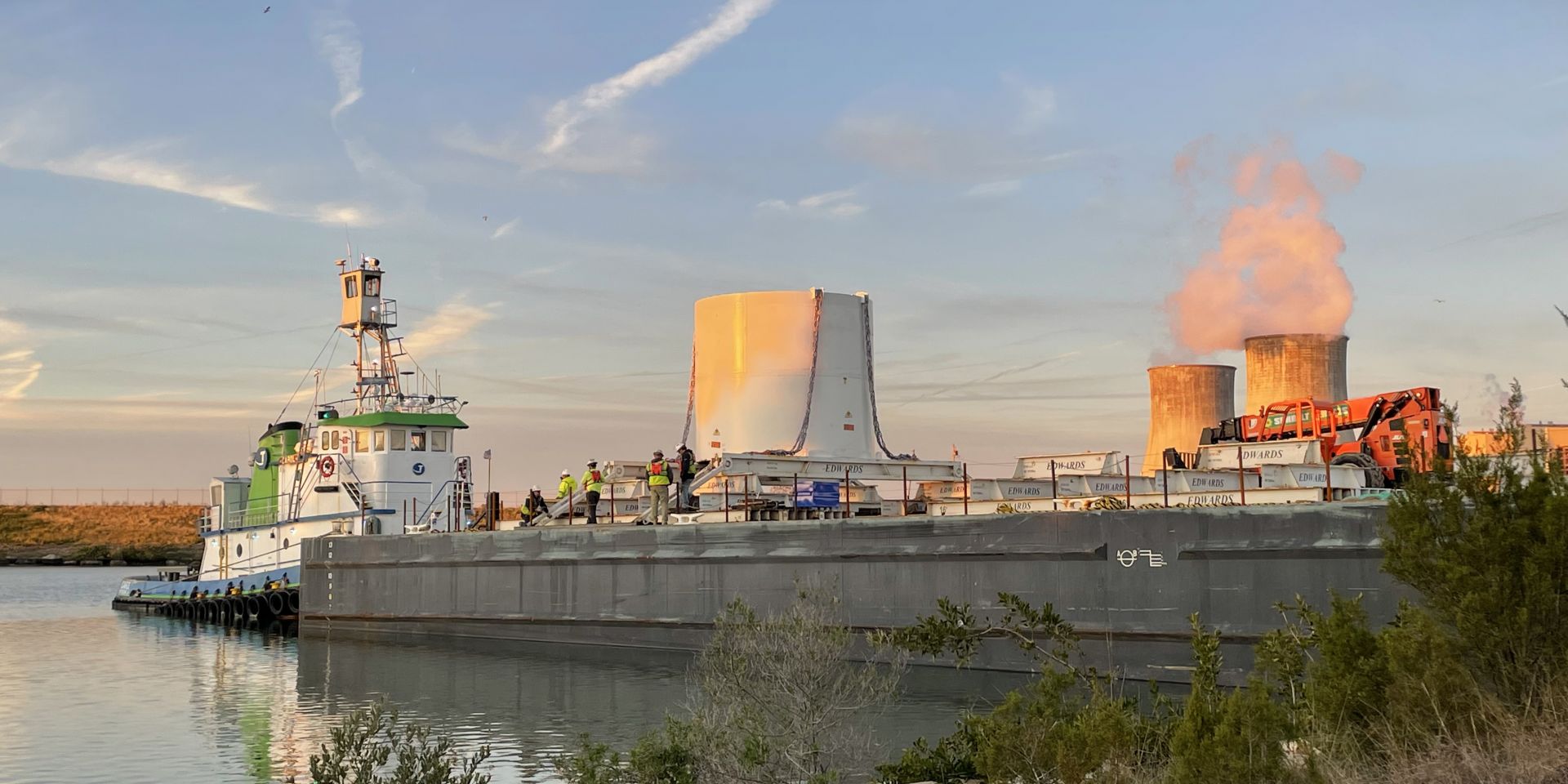
The Optimized Segmentation process patented by Orano Decommissioning Services was successfully implemented for the first time at the Crystal River Unit 3 (CR-3) decommissioning project in Florida [1]. Using this approach, Orano was able to avoid the time- and resource-intensive process of packaging components into numerous standardized waste containers and significantly reduced the required segmentation activities.
The process also greatly reduced the multiple waste shipments of all low-level radioactive waste from the reactor vessel internals (RVI) and the reactor vessel (RV). Instead, only four custom-designed packages—top, middle, bottom, and closure head—were required to dispose of the LLW generated from the removal of the RV and RVI components, which were loaded and secured on a single barge for transportation from Florida’s west coast to Texas across the Gulf of Mexico (Fig. 1). The packages were then separately transported west by road across Texas to Waste Control Specialists’ (WCS) disposal facility in Andrews County, Texas.
With the precedence of this first successful project, completed in 2024, Orano feels that the approval of waste packages by the Nuclear Regulatory Commission and their disposal can be routine in the future. For waste packages going to WCS, the transportation route from a Texas port to the WCS facility for Orano’s packages can be used as a model for permitting of all future shipments. Transportation routes to the EnergySolutions’ disposal facility at Clive, Utah, may be permitted in the future, as well.
In addition to the four packages shipped by barge, there were 10 additional large component shipments, which contained components from the CR-3 reactor coolant system, including one pressurizer, four reactor coolant pumps and four motors, and the RV integrated head assembly (control rod drives and service structure). These components were transported by rail to WCS in compliance with Department of Transportation industrial package regulations [2].
Finally, Orano worked closely with the WCS team to dispose of all shipped components. All components met the exempt disposal criteria (including the pressurizer) except for the reactor vessel’s closure head, top package, and bottom package, which were classified as Class A disposal, and the reactor’s middle package, which was classified as Class B/C disposal.
The packages
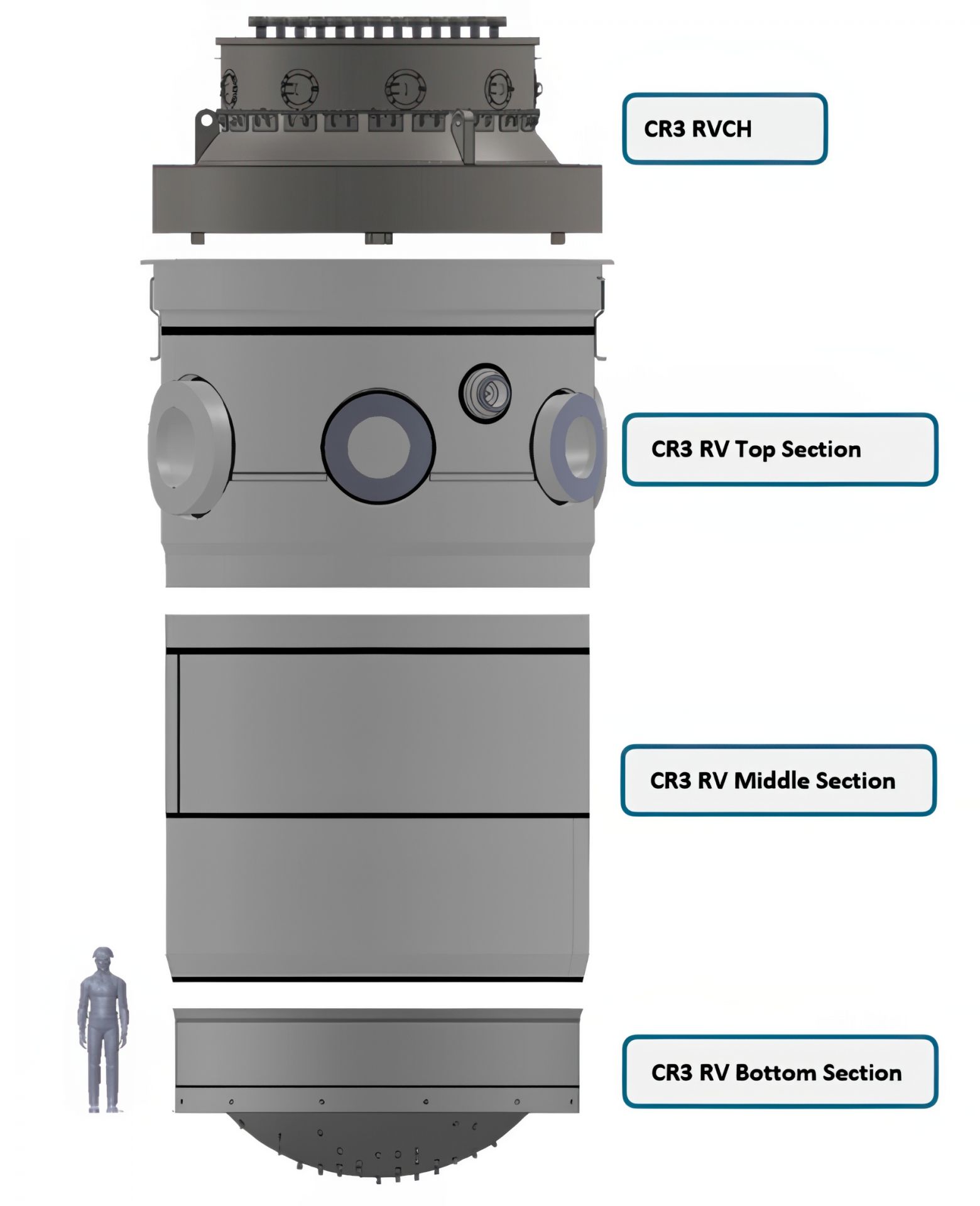
Fig. 1: CR-3 RV segments.
The segmented RVI components that were determined to be not greater-than-Class C waste were segregated and repacked (reintroduced) inside the RV using a precisely engineered placement strategy based on each component’s waste characterization. The repackaged RVI inside the RV were then immobilized using low-density cellular concrete (LDCC), specifically engineered to achieve the package requirements, ALARA (as low as reasonably achievable) goals, and transportation limits.
The solid, LDCC-filled RV packed with waste was subsequently segmented into three large sections (top, middle, bottom), consistent with the optimized waste distribution plan. Each section was packaged and shipped individually in tailor-made containers designed by Orano (top and middle package) or by using custom-designed supersacks (bottom package) to safely transport and dispose of the waste in compliance with relevant regulations (NRC for Type B shipment, DOT for industrial package) and the disposal site’s waste acceptance criteria.
As planned, only the middle RV section (of the three segmented RV sections) required an NRC-approved Type B package for shipment in accordance with 10 CFR Part 71. The optimized waste characteristics in the two remaining reactor vessel segments—the bottom and top sections—as well as the reactor closure head, only required packaging to comply with the DOT industrial package regulations (49 CFR Part 173).
The four packages were handled at the Crystal River site using heavy-load-capacity self-propelled modular transporters (SPMT) before being loaded onto the barge.
The specifications for the RV components are listed in Table 1.
Table 1. RV package specifications
Description | Qualification | Contents | Weight (lbs.) | Total Activity/ Co-60 Activity (Ci) | |
---|---|---|---|---|---|
Reactor Vessel Closure Head (RVCH) Package | UN2913/Radioactive Material, Surface Contaminated Object (SCO-II) fissile-excepted | DOT Industrial Package Type 1 (IP-1) Qualification | Consists of bottom support assembly, RVCH, top shield plate, and a custom-made bag | ~190,000 | 0.46/0.27 |
CR-3 Top Package (CR-3TP) | UN3321/Radioactive Material, Low Specific Activity (LSA-II) fissile-excepted with 10 CFR 37 | DOT Industrial Package Type 2 (IP-2) Qualification | Consists of outer cylindrical container, ~RV top third with RV internals (RVCH bolting flange to just below RV nozzles), and low-density cellular concrete | ~610,000 | 12.3/6.0 |
CR-3 Middle Package (CR-3MP) | UN2916/Radioactive Material, Type B(U) package fissile-excepted | NRC Type B Special Package Authorization Qualification – Docket No. 71-9393 | Consists of outer cylindrical container, ~RV middle third with RV internals (extending over the active fuel region), and low-density cellular concrete | ~720,000 | 15,741/8,190 |
CR-3 Bottom Package (CR-3BP) | UN3321/Radioactive Material, Low Specific Activity (LSA-II) fissile-excepted | DOT Industrial Package Type 1 (IP-1) Qualification | Consists of bottom support assembly, RV bottom third (lower dome) with RV internals, top shield plate, and low-density cellular concrete, and a custom-made bag | ~135,000 | 0.80/0.38 |
Reactor vessel removal
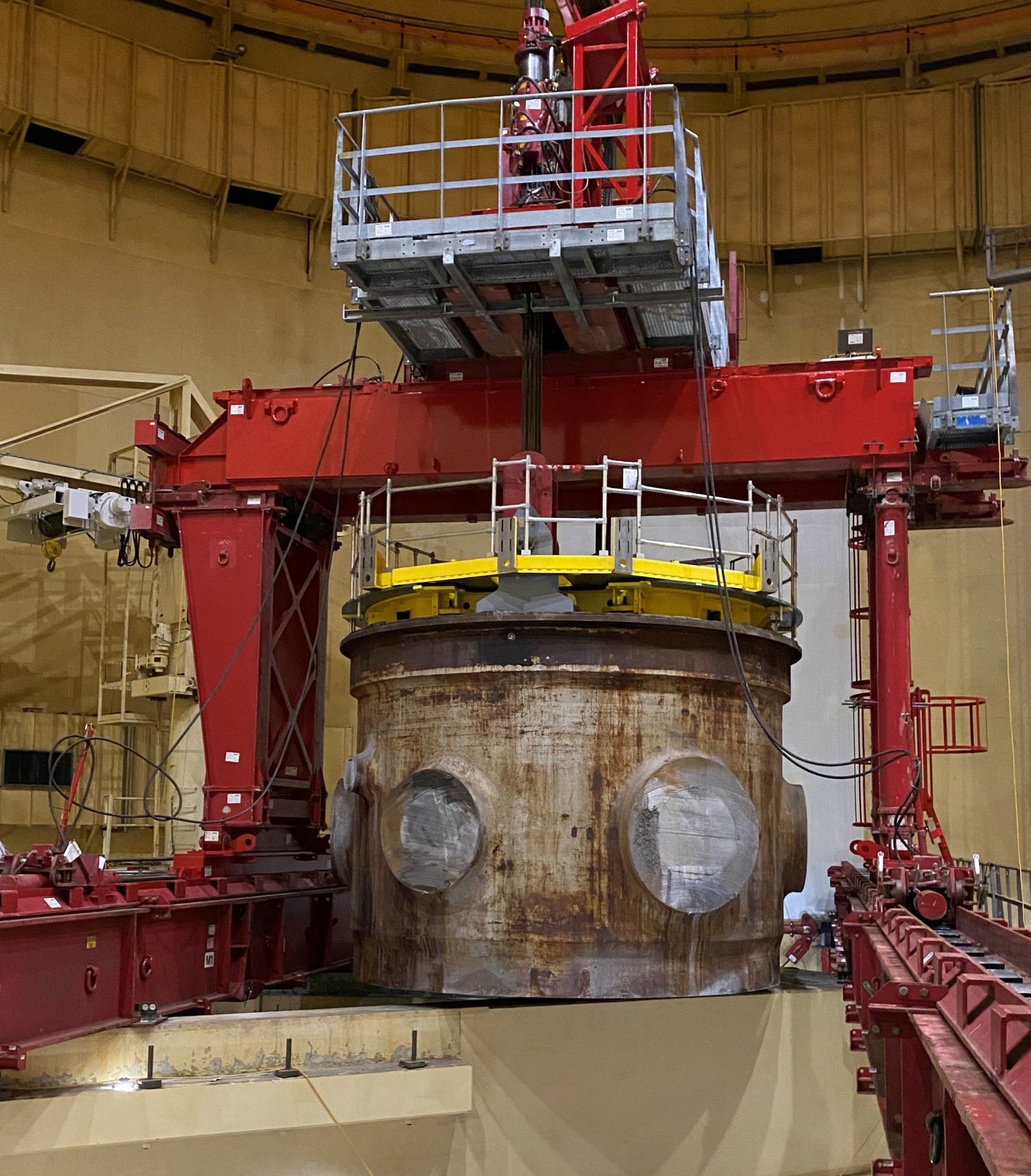
The CR-3 RV top segment is removed from the reactor cavity.
The RV closure head (RVCH) package frame designed by Orano served many purposes, including for both temporary storage on-site and transportation by barge and over-the-road open transporter vehicle. The RVCH had a waste classification as exempt and was considered a surface contaminated object (SCO-II), which was handled, packaged, shipped, and disposed of as one piece, after the control rod drive mechanisms and service structure had been removed. A custom-designed supersack was its final packaging.
After removal of the RVCH service structure, the RVCH was lifted and loaded onto the RVCH bottom support frame with an awaiting supersack using the conventional containment building overhead crane. A fabricated top shield plate was placed onto the top surface of the RVCH for dose rate control purposes. The bag was then used to cover the entire RVCH and the shielding plate. The RVCH was then transferred outside the reactor building for storage.
The CR-3 top package (CR-3TP) design and fabrication followed the guidance of ASME B&PV Code, Section VIII, Division 1 for pressure vessels fabricated by welding [4]. This code was selected for this package based on the total activity value of the payload, which classified this package as a Category III container in accordance with NRC regulatory guidance documents. The CR-3TP complied with the DOT industrial packaging Type 2 (IP-2) performance, technical, and regulatory requirements. The CR-3TP contained the top section of the RV, extending from the RVCH bolting flange to just below the RV nozzles. In addition, the CR-3TP contained irradiated RVI remnants, including the top of the plenum assembly and core support shield.
After loading within the containment building was completed, the CR-3TP was transferred outside to place the lid and then moved into a temporary structure for closure weld activities. The top cover weld was completed in the field. The CR-3TP package was then transferred to storage.
The CR-3 middle package (CR-3MP) design and fabrication followed the guidance of ASME B&PV Code, Section III, Division 1, Subsection ND. This code was selected for this package based on the bounding activity value of the payload, which classified this package as a Category II container in accordance with NRC guidance.
The physical design features of the CR-3MP were remarkably similar to the CR-3TP, except it is of thicker steel material construction to meet NRC 10 CFR Part 71 design criteria. The contents of this container consisted of the most radioactive RVI components of solid physical form. This was a Type B package, and an application was submitted to the NRC to obtain a special package authorization (SPA) in September 2021. This process allows organizations to transport certain types of radioactive materials in special packages. The NRC approved the application and issued the SPA license, including the specific conditions and limitations, in August 2023.
The CR-3MP was shipped under NRC regulations per 10 CFR Part 71 [3]. An amendment was issued in April 2024 to allow for a longer shipping duration. The CR-3MP contained the middle section of the RV extending from just below the RV nozzles to just below the active fuel region. By design, the CR-3MP contained the most radioactive irradiated RVI remnants within the smallest volume.
The CR-3 mausoleum storage for all four RV packages prior to shipment.
After loading within the containment building was completed, the CR-3MP was transferred outside to place the lid and then moved into a temporary structure for closure weld activities. The top cover weld was completed in the field, and the package was transferred to storage. Just prior to transport, the vent port was plugged and welded as the final closure weld.
Like the RVCH, the CR-3 bottom package (CR-3BP) frame was designed by Orano to be adequate for both storage and transportation. The CR-3BP had a waste classification of Class A, which was handled, packaged, shipped, and disposed of as one piece. The CR-3BP was packaged into a custom-designed supersack. The package contained the bottom bowl section of the RV.
After segmentation, the RV bottom section was lifted and loaded onto the CR-3BP frame with an awaiting supersack using the conventional reactor building overhead crane. A fabricated top shield plate was placed and secured onto the top surface of the bottom section for dose rate control purposes. The bag was then used to cover the entire bottom section with the shielding plate. The CR-3BP was then transferred outside the reactor building for storage to await transportation.
The transport
In early 2024, haul path modifications and upgrades were performed at the Crystal River site. The transfer haul path required fill to be brought in and compacted to support the expected axle loads. The site’s barge slip was prepared along with precaution being taken on protected species and vegetation, including scallops and mangroves. The barge officially arrived at the site on January 16, 2024. The barge was docked and secured, and the barge team immediately began installing the barge ramps and preparing for receipt of the RV packages.
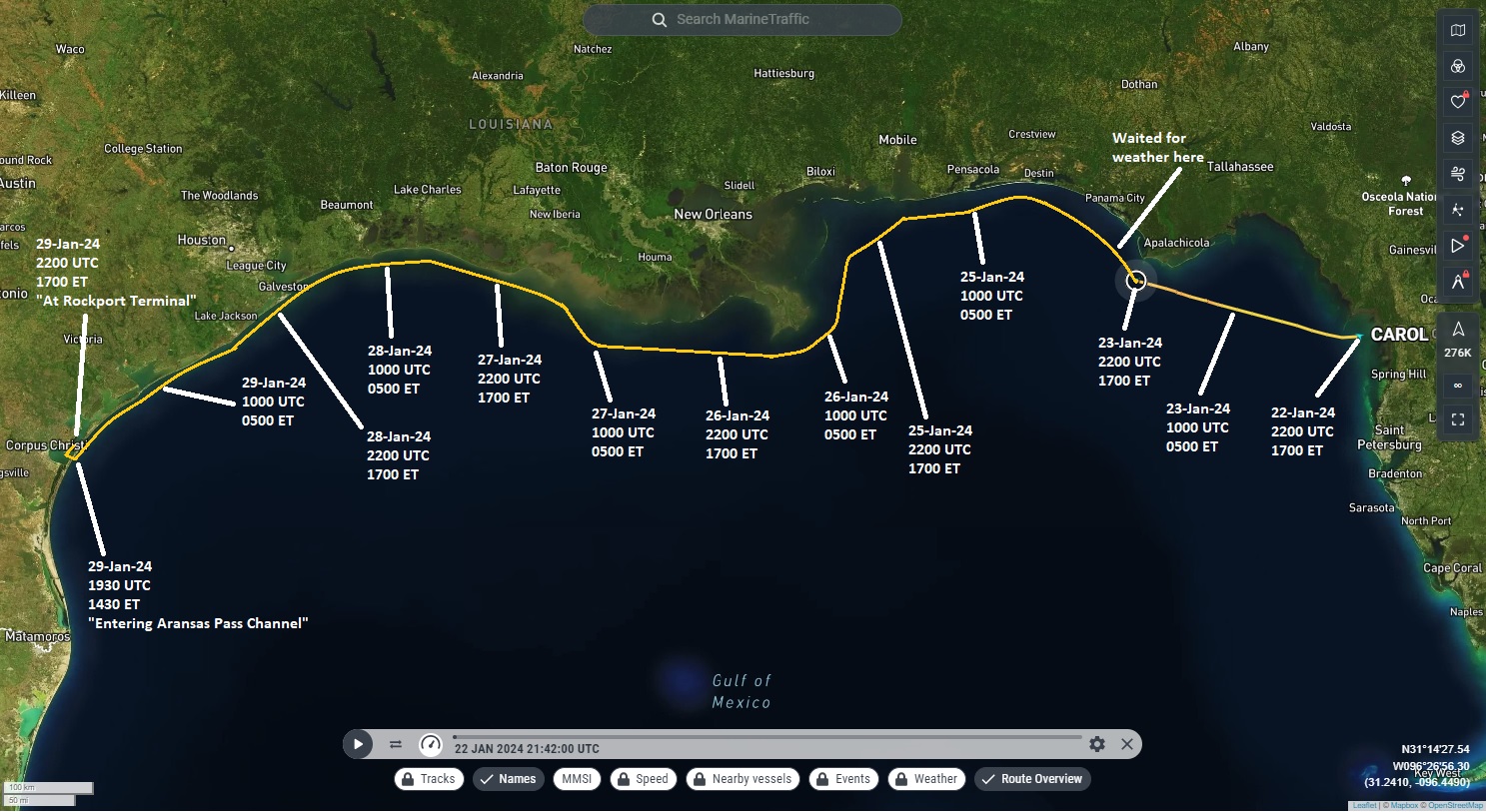
The barge travel path from Florida to Texas.
On January 17, the CR-3MP, the first package to be loaded, was removed from the mausoleum where it was being stored and transferred to the barge by a double-wide SPMT, with a total package weight of 716,000 pounds. Likewise, the CR-3TP, the second package to be loaded, was removed from the mausoleum and transferred to the barge on January 19 by a double-wide SPMT, with a total package weight of 608,000 lbs. The RVCH was then removed from the mausoleum the following day and transferred to the barge by a single-wide SPMT, with a total package weight of 186,000 lbs.
Finally, on January 21, the CR-3BP, the fourth and final package to be loaded, was removed from the mausoleum and transferred to the barge by a single-wide SPMT, with a total package weight of 132,000 lbs. All four RV packages were secured to the barge, the ramps were removed, and the barge was readied for voyage.
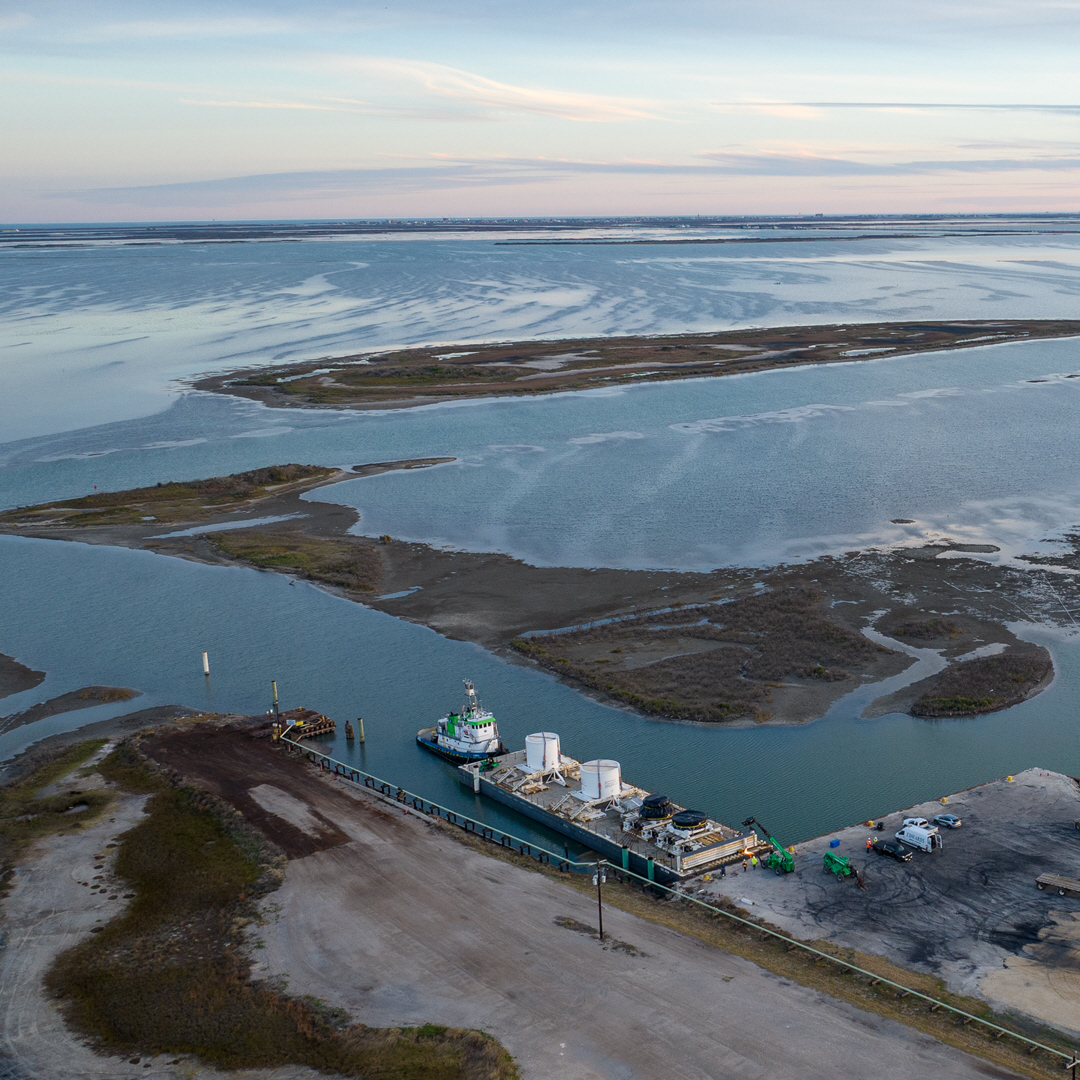
The barge with the four RV packages arrives at the Texas port at Rockport after crossing the Gulf of Mexico.
The RVCH and CR-3BP are staged in Rockport prior to being shipped to WCS.
On January 22, six days after the barge arrived at the west Florida site, the barge disconnected from the shore and started its journey. The barge traveled across the Gulf of Mexico along the Intercoastal Waterway. Several storms caused the barge to stop and wait, but exactly seven days later, the barge arrived at the Texas port at Rockport.
Upon arrival at Rockport, the inverse operations of the barge loading process were performed. The RV packages were unloaded and staged in a transloading position until the transport vehicle was available. As the barge was not grounded, such as it was at Crystal River, ballast pumps were used on the barge to displace water to allow the RV packages to be unloaded.
The RVCH and CR-3BP were placed in a newly graded port area and placed on stands, which allowed the packages to be high enough to be able to be transitioned to the transporter without any lifting. The CR-3MP and CR-3TP were positioned in a port area to allow for easier maneuvering of the Goldhofer Faktor 5 trailer assembly, due to the sheer size of this conveyance.
The RVCH departed Rockport on February 3 and arrived at WCS on February 5, while the CR-3BP departed on February 12 and arrived at WCS on the 14th. Each package traveled approximately 800 miles over a three-day transport. The CR-3BP and RVCH were officially disposed of at the WCS facility on April 23 and April 29, respectively.
The CR-3TP and CR-3MP required additional transportation permit approval, as well as the use of a heavy-haul transportation system to transport the packages via commercial road. The state of Texas Department of Motor Vehicles oversize/overweight permit for the Type B CR-3MP was received on April 30, while the oversize/overweight permit for the CR-3TP, the fourth and last package, was received on July 25.
The CR-3MP departed Rockport on April 30 and arrived at WCS on June 4. The large heavy-haul transport system returned to Rockport to transport the CR-3TP, which departed Rockport on July 25 and arrived at WCS on August 23.
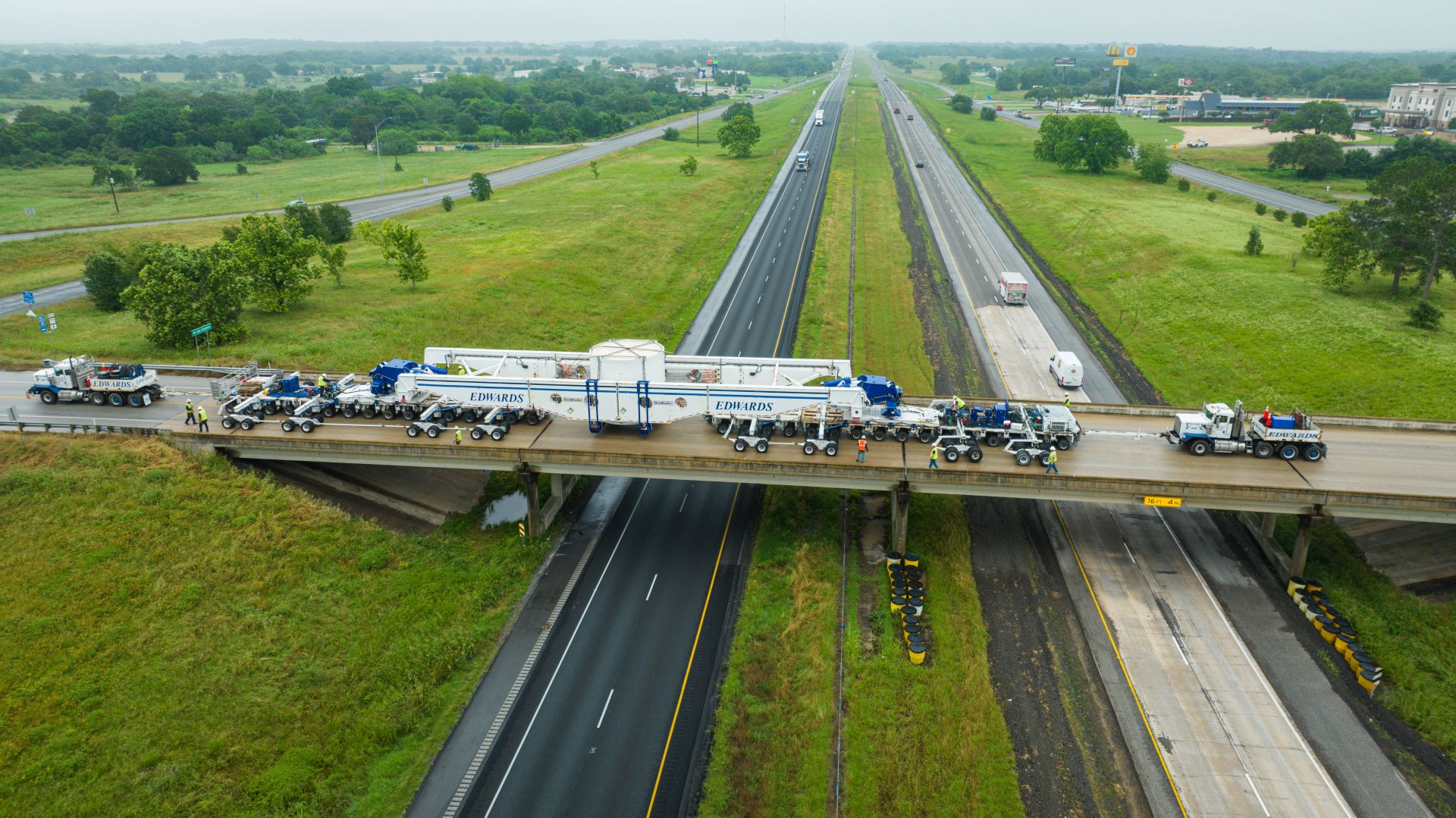
With wing dollies extended to further distribute the weight, a package containing the CR-3 segmented reactor vessel slowly progresses across a bridge in Texas.
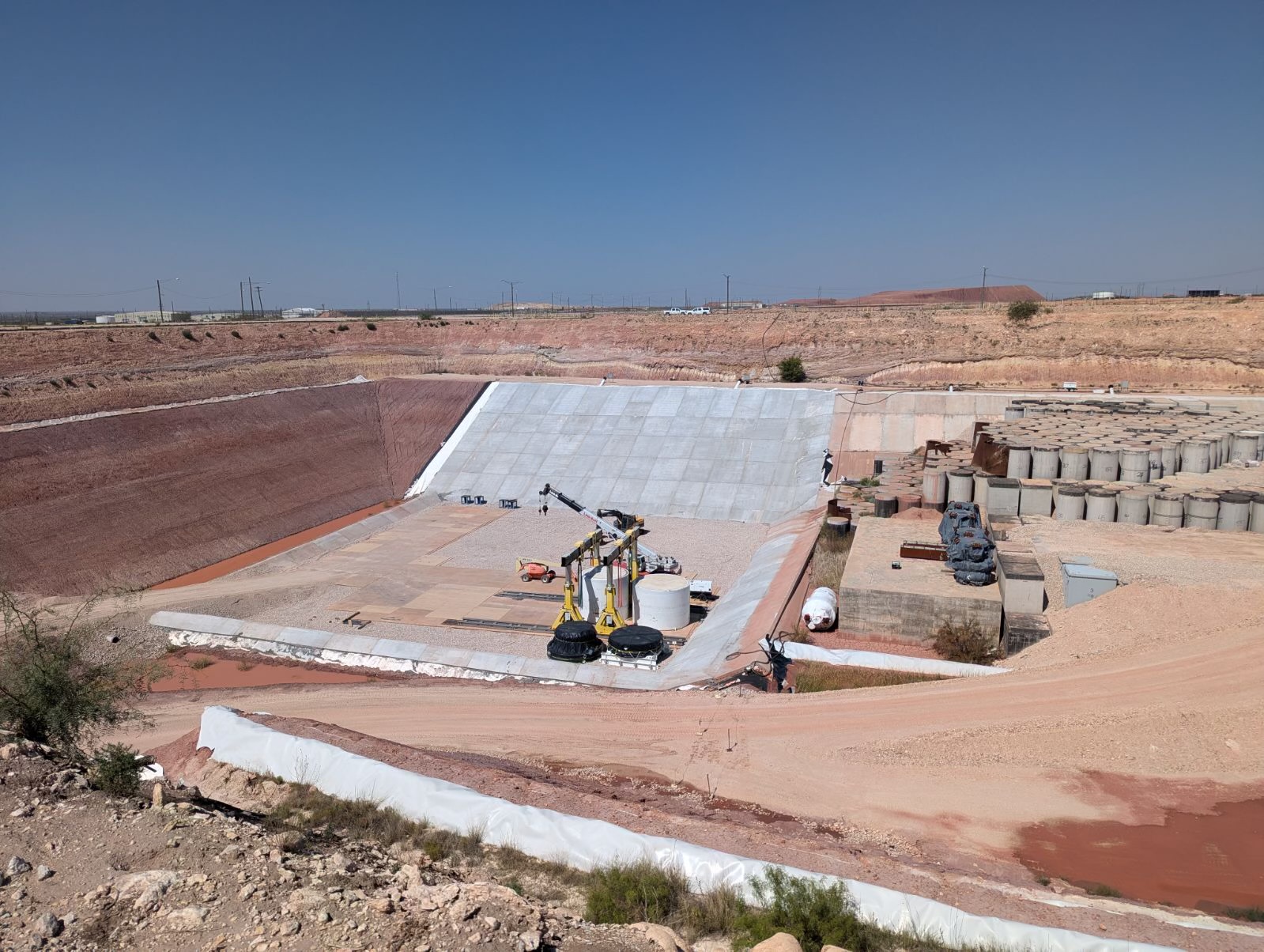
The CR-3TP and CR-3MP are interred at WCS.
A few key statistics of the transports:
Dollies were used 151 times for each shipment.
Deployed bridge jumper systems for traversing three bridges for CR-3MP and two bridges for CR-3TP.
Performed two contraflow (wrong way) traffic events per shipment.
Shut down a portion of one major interstate for each shipment (I-20).
73 road signs were removed and restored during each shipment.
15 support vehicles including 22 crew members were included in the convoy for each shipment.
Eight Texas districts were passed through during the over-the-road transport.
Approximately 970 miles were traveled per package over about a 30-day duration.
The CR-3TP and CR-3MP were officially disposed of at the WCS facility on September 6 and September 9, respectively. The four RV packages were the first components to be placed into a recent cell expansion completed by the WCS team.
The packaging and transportation of CR-3’s RV components, including the top, middle, and bottom packages, followed meticulous planning, ensuring each shipment adhered to rigorous standards. Coordination with various stakeholders was crucial for securing specialized transport vehicles and permits for heavy-haul transportation. Despite challenges such as weather disruptions and regulatory hurdles, the project progressed smoothly, with final disposal completed at the WCS facility in Texas.
Richard “Ricky” Furr is project manager, Larry McDougal is a project manager, and John Mayer is the engineering manager with Orano DS.
References
- “Optimized Segmentation of the Crystal River Unit 3 Reactor,” WM2024 Conference, March 2024.
- Code of Federal Regulations, Title 49, Transportation, Subtitle B: “Other Regulations Relating to Transportation (Continued)” (Parts 100–1699); Chapter I: “Pipeline and Hazardous Materials Safety Administration, Department of Transportation” (Parts 100–199); Subchapter C: “Hazardous Materials Regulations,” October 2020.
- NRC, 10 CFR Part 71, “Packaging and Transportation of Radioactive Material.”
- “Packaging of the Crystal River Unit 3 Reactor Segments–24184,” WM2024 Conference, March 2024.