Advanced Nuclear Fuel Cladding: Innovative Materials Enhance Fleet Safety and Performance
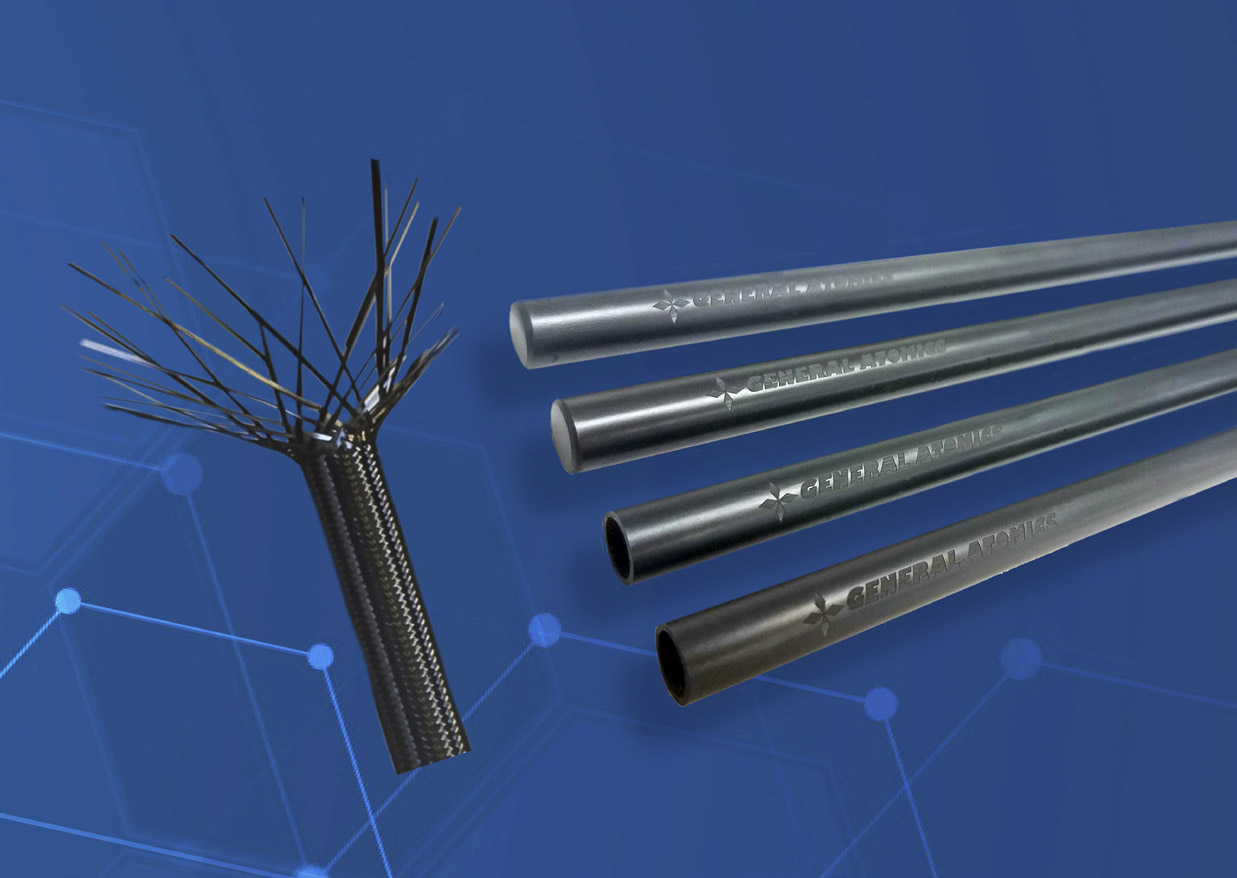
General Atomics Electromagnetic Systems (GA-EMS) is charting a path to advance SiGA® silicon carbide (SiC) ceramic matrix composite cladding for nuclear fuel rods to provide enhanced safety, improved operational performance, and economics benefits for the existing Light Water Reactor (LWR) fleet as well as future advanced reactor systems.
Transforming How Nuclear Fuels Are Made
GA-EMS’ SiGA cladding is a multi-layer structure, designed from the ground up for in-core performance. SiC composites have excellent resistance to neutron irradiation and high temperatures compared to existing metal cladding structures.
The SiGA cladding tube is comprised of an inner composite layer and an outer monolithic SiC layer. The inner composite is reinforced with SiC fibers to provide strength and toughness. The outer layer is a dense SiC monolith that retains the fuel and fission products produced during operation. All aspects of the technology, from the orientation of the reinforcing fibers to the microstructure of the outer SiC monolith, are carefully modeled and tested to provide unrivaled high temperature performance and in-core stability.
SiGA fuel rods are sealed on both ends employing a proprietary SiC joining approach. This ensures the cladding remains strong and intact withstanding temperatures up to 1900° C without melting and offers an orders of magnitude reduction in hydrogen production due to steam interaction in the unlikely event of loss of cooling. Unlike conventional zircaloy metal fuel rod claddings, which tend to soften at 800° C and then fail, SiGA rods maintain a coolable geometry to significantly reduce the risk of failure and allow for longer response times at high temperatures in accident situations.
In addition to higher performance and enhanced safety, SiC’s in-core stability can reduce the frequency for refueling existing LWRs, which can improve nuclear power plant economics through longer fuel cycles and subsequent reduction in overall operating costs. Combined, these same properties make SiC composites a promising material to enable future advanced, high temperature reactor systems, such as the GA-EMS Fast Modular Reactor (FMR) - a high temperature gascooled fast reactor.
Performance Testing Under Normal and Accident Conditions
Demonstration testing yields exciting progress.
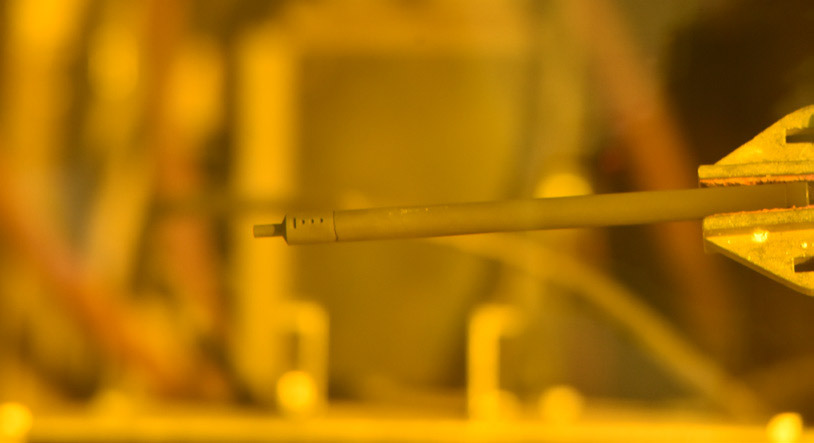
SiGA Fuel Rod Shown Intact After 120 Days of Irradiation.
SiGA rods were exposed to high temperature steam conditions alongside zircaloy cladded rods. The SiGA rods remained intact under loss-of-coolant conditions which caused zircaloy rods to fail and burst under the same conditions.
View the test video at:
www.energy.gov/ne/articles/generalatomics-completes-first-round-testingnew-ceramic-fuel-cladding
Accelerating Progress toward Licensing and Qualification
GA-EMS follows the Accelerated Fuel Qualification (AFQ) framework, which is a methodology that leverages physics-informed multi-scale modeling along with targeted empirical test data to reduce the time and cost of licensing and qualification of new nuclear fuel systems, while maintaining the overall nuclear power plant safety case. Following this methodology, SiGA material is being irradiated at test reactors located at Oak Ridge National Laboratory (ORNL), Massachusetts Institute of Technology (MIT), and Idaho National Labs, with each irradiation being informed by advanced modeling to verify model assumptions and establish performance limits of the cladding.
Unfueled SiGA rodlets passed a critical milestone in 2024 with successful performance in the first irradiation tests in the Advanced Test Reactor (ATR) at Idaho National Laboratory (INL), and in the Massachusetts Institute of Technology Reactor (MITR) at MIT in which rodlets maintained gas-tightness and retained physical integrity after 120-days in the representative Pressurized Water Reactor (PWR) water environments. The resulting data shows the SiGA cladding performs as designed. GA-EMS is conducting detailed examinations and evaluations of post-test data to update and inform models in preparation for the initial fueled testing of SiGA cladding.
2025 and Beyond: The Path to Commercialization
GA-EMS continues to partner with the DOE, fuel vendors, utilities, and the national labs to accelerate SiGA cladding development. This path includes process scaling to full-length, 12-foot commercial cladding lengths, advanced out-of-pile testing, development of multi-scale models to support AFQ and progressive irradiation testing on a series of unfueled, non-uranium fueled, and uranium fueled SiGA rods. Significant progress is being made in these areas as the technology advances to irradiation in commercial power reactors using full-length fuel rods by the end of this decade.
As the nuclear industry modernizes, SiC composite cladding materials can help realize the untapped potential of the existing reactor fleet to better utilize nuclear fuel while increasing the margin for safety. GA-EMS is progressing its manufacturing capabilities to realize a sustained domestic supply of SiGA fuel cladding material to support the current and future nuclear reactor fleet, with the goal of commercialization in the 2030s.
www.ga.com/nuclear-fission/accident-tolerant-fuel
www.ga.com/ems