General Atomics tests fuel as space nuclear propulsion R&D powers on
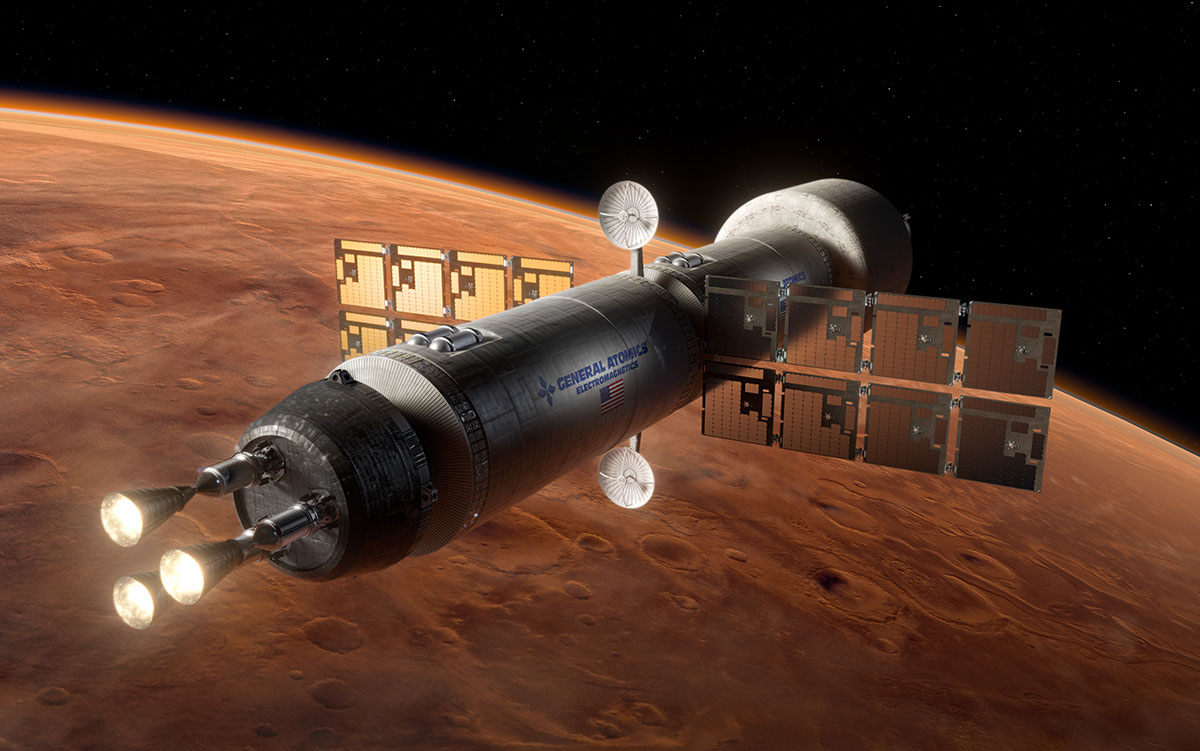
General Atomics Electromagnetic Systems (GA-EMS) has announced that it has subjected nuclear thermal propulsion (NTP) fuel samples to several “high-impact” tests at NASA’s Marshall Space Flight Center (MSFC) in Huntsville, Ala. That news comes as NASA, the Department of Defense, the Department of Energy, and multiple nuclear and space technology companies continue to build on recent progress in nuclear thermal rocket design and demonstration.
Testing: GA-EMS used NASA MSFC’s compact fuel element environmental test (CFEET) to verify that its fuel can withstand extreme conditions inside a compact, high-temperature reactor fit for space conditions, according to a January 20 company announcement.
Hot hydrogen flowed through the samples as they were subjected to six thermal cycles that ramped up to a peak temperature of 2,600 K (about 4,220°F). Each cycle included a 20-minute hold at peak performance to test the effectiveness of shielding to protect the fuel from erosion and degradation by the hydrogen. According to GA-EMA, additional tests of “varying protective features” were performed to test different materials under reactor-like conditions.
“To the best of our knowledge, we are the first company to use the compact fuel element environmental test (CFEET) facility at NASA MSFC to successfully test and demonstrate the survivability of fuel after thermal cycling in hydrogen representative temperatures and ramp rates,” said Christina Back, vice president of GA-EMS Nuclear Technologies and Materials.
Deemed a success: “The recent testing results represent a critical milestone in the successful demonstration of fuel design for NTP reactors,” said Scott Forney, president of GA-EMS. “Fuel must survive extremely high temperatures and the hot hydrogen gas environment that an NTP reactor operating in space would typically encounter. We’re very encouraged by the positive test results proving the fuel can survive these operational conditions, moving us closer to realizing the potential of safe, reliable nuclear thermal propulsion for cislunar and deep space missions.”
Back explained that GA-EMS has previously conducted high-temperature tests of its fuel design in a nonhydrogen environment at GA-EMS laboratories, confirming that the fuel “performed exceptionally well at temperatures up to 3,000 K, which would enable the NTP system to be two-to-three times more efficient than conventional chemical rocket engines.”
NTP under contract: The testing was conducted by GA-EMS for NASA under a contract managed by Battelle and Idaho National Laboratory. In July 2021, GA-EMS, BWX Technologies, and Ultra Safe Nuclear were each awarded contracts to produce a conceptual reactor design.
General Atomics also answered the call from the Defense Advanced Research Projects Agency (DARPA) for the design of a reactor that could power DRACO, the Demonstration Rocket for Agile Cislunar Operation, and was awarded the Track A Phase 1 contract in April 2021. While GA-EMS submitted a baseline design under that contract in the fall of 2022, the Phase 2 reactor design contract was awarded to BWXT in July 2023.
While DRACO is progressing—though at a pace reported to put its most recent launch target of fiscal year 2027 in doubt—DARPA issued a request for information in December looking for “innovative and revolutionary solutions” that can “leverage the current DRACO reactor design and development effort” and “enhance transition to future missions.” The solicitation closed January 21.
Not GA’s first space race: Work by GA-EMS on space nuclear propulsion goes back to the 1950s, and the company’s latest NTP reactor concept draws on its experience on Project Rover in the 1960s. According to GA the company fabricated about 6 metric tons of nuclear fuel kernels for the project.
GA-EMS’s recent work—and all recent nuclear thermal propulsion work by NASA, DARPA, and the DOE—aims to address issues in historical nuclear rocket designs, such as fuel element corrosion. And this time, they are doing it with high-assay low-enriched uranium, not high-enriched uranium.